The manufacturing industry has always been a cornerstone of economic growth and development. However, in 2023, amidst rapid technological advancements and changing market dynamics, the importance of manufacturing skills in the industry has reached new heights. With increasing automation, advanced machinery, and complex processes, organizations require a highly skilled workforce with proficient manufacturing and production skills to stay competitive.
Organizations are seeking employees who possess a diverse range of expertise to tackle evolving challenges and seize opportunities. Skilled professionals with adaptability, versatility, and expertise in various aspects of manufacturing skills are highly sought after by organizations.
In this article, we will explore the in-demand skills in manufacturing. We will provide a comprehensive overview of the 10 most sought-after manufacturing skills, offer practical advice on skill enhancement, and provide useful tips on effectively showcasing your skills during the hiring process.
What Defines Manufacturing Job Skills?
Manufacturing job skills are vital to a professional's success within the manufacturing industry. These manufacturing skills encompass a combination of technical and soft skills that enable individuals to navigate the evolving landscape. For example, the industry is experiencing a shift towards technology-driven automated procedures, and traditional assembly lines are being replaced.
To stay ahead in this transformation, professionals must possess a diverse skill set, including engineering expertise, proficiency in traditional manufacturing techniques, and effective soft skills. These manufacturing skills equip professionals to adapt to changing demands, drive innovation, and excel in their manufacturing roles.
10 Most In-demand Skills Needed for Manufacturing Industry
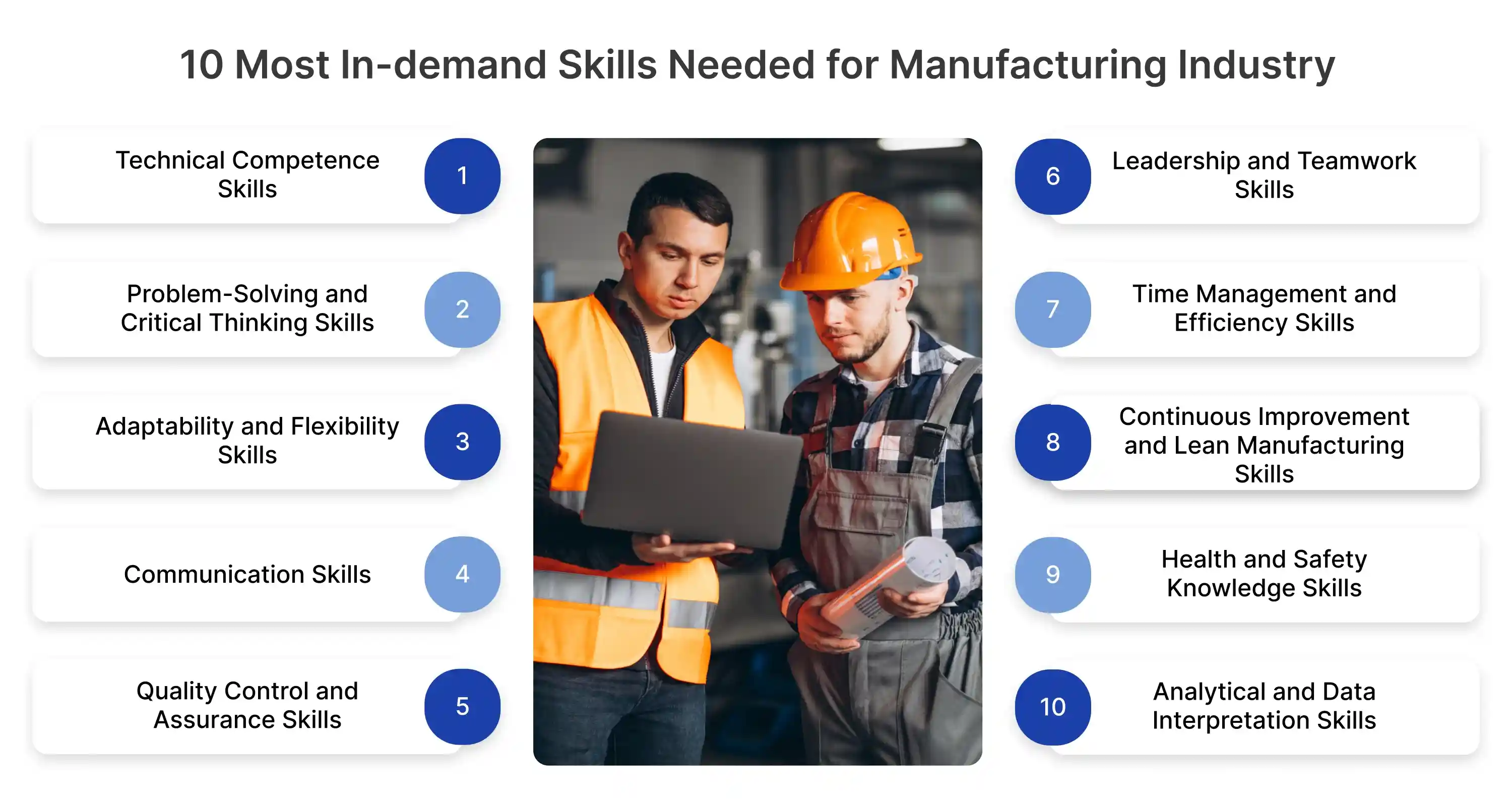
1. Technical Competence Skills
In today's competitive business landscape, staying ahead requires organizations to invest in their employees' continuous growth and development. One crucial aspect of this is enhancing technical competence through targeted training programs. By upskilling your employees in technical areas, you can unlock a multitude of benefits that directly contribute to business growth.
Technical competence forms the foundation for success in various roles within your organization. It involves mastering specific technical knowledge and expertise necessary to perform tasks efficiently and effectively. This includes understanding industry-specific technologies, tools, and processes relevant to your business.
Market Growth
According to a report by Deloitte, technical competence in manufacturing skills has played a significant role in the growth of the manufacturing industry. The demand for skilled technical workers has increased with AI, robotics, and IoT adoption.
The skills gap in the industry may leave 2.4 million positions unfilled between 2018 and 2028, with an economic impact of 2.5 trillion dollars. Industry experts have also highlighted the need for workers with the right skills in manufacturing.
2. Problem-Solving and Critical Thinking Skills
To achieve sustainable business growth, organizations must invest in upskilling their employees. For example, one in-demand skill that holds immense value in the manufacturing industry is problem-solving and critical thinking skills. Organizations can empower their workforce to tackle challenges head-on and drive innovation by providing targeted training programs to develop these skills, ultimately fueling business growth.
Importance of Problem-Solving Skills in Manufacturing
Problem-solving skills are crucial for success in the manufacturing industry. They enable employees to identify and address complex issues during production processes, ensuring smooth operations. Effective problem-solving minimizes downtime, optimizes resource utilization, and improves productivity.
Moreover, problem-solving skills foster a culture of innovation and adaptability within organizations. They encourage employees to think creatively and explore alternative approaches, leading to the development of new ideas, streamlined workflows, and enhanced product quality. As a result, organizations prioritizing problem-solving skills are better equipped to meet customer demands, stay ahead of competitors, and drive market growth.
Strategies for Developing Critical Thinking Abilities:
Critical thinking and problem-solving skills are important for success in Industry 4.0, and high innovators in the manufacturing industry prioritize their development.
3. Communication Skills
Investing in an instructor-end training program to enhance employee communication skills is essential for organizations seeking sustainable growth. By equipping your workforce with strong communication abilities, you can foster collaboration, streamline operations, and positively impact business growth.
Effective Communication Skills in Manufacturing Industry
Clear and efficient communication skills are vital in the manufacturing industry. It ensures smooth coordination between different teams, minimizes errors, and enhances productivity. Furthermore, in a fast-paced setting with various stakeholders involved, effective communication helps in the following ways.
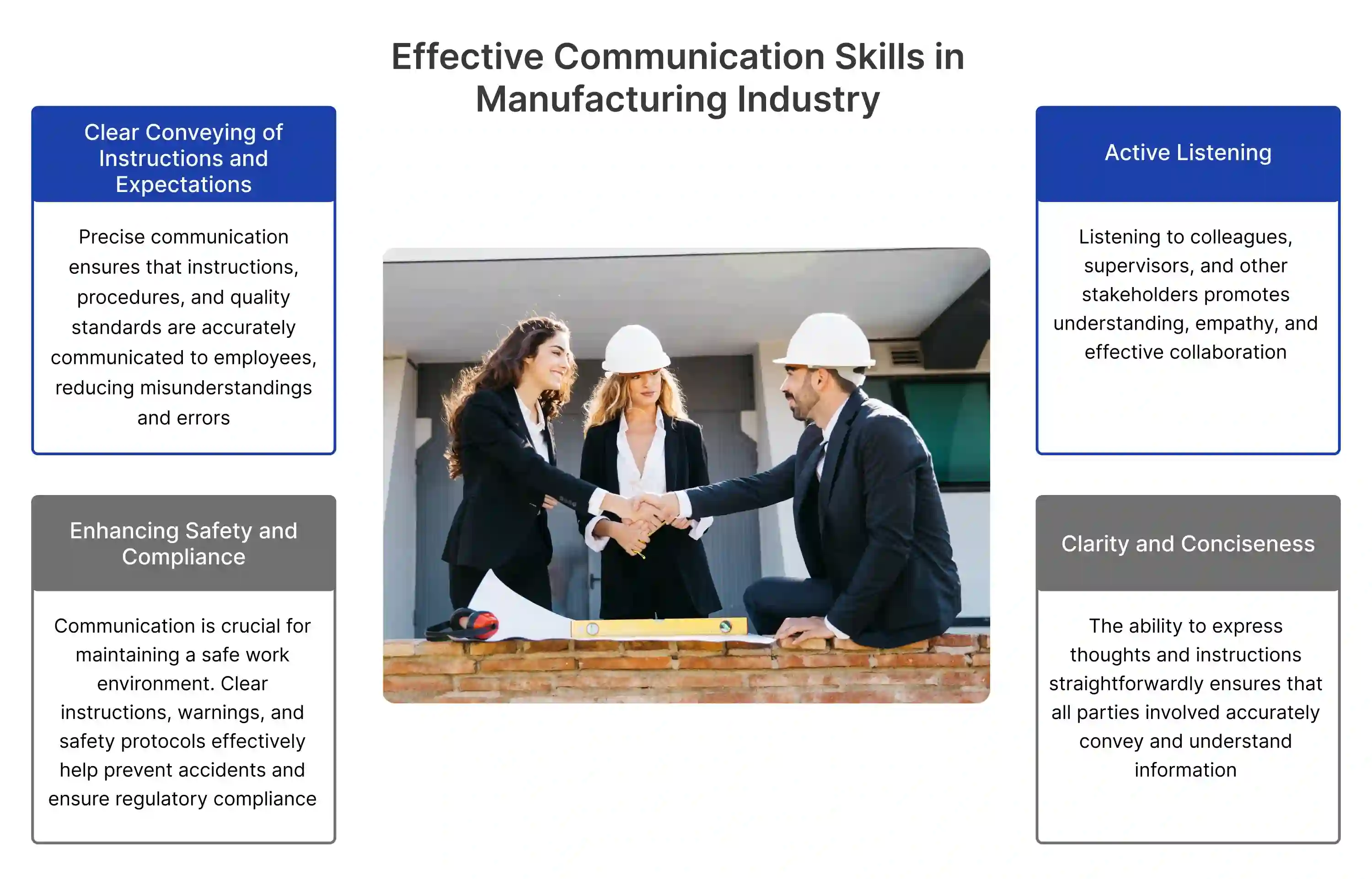
Emphasizing the importance of communication skills and providing targeted training programs will enable your workforce to communicate effectively, paving the way for sustainable growth and continued success in the competitive market.
Growth Market
According to Future State 2030 by KPMG International's research on megatrends that will impact governments and public sector policymakers through 2030, effective communication skills are crucial for achieving leading practice government that includes greater cooperation, promoting behavioral change, and using technology more effectively. Communication skills, emotional intelligence, and collaboration are essential for success in the manufacturing industry.
4. Adaptability and Flexibility Skills
Manufacturing processes continuously evolve due to technological advancements, market demands, and industry trends. To remain competitive, organizations must recognize the importance of adaptability and flexibility skills in the following areas:
- Embracing Technological Advancements: Employees with adaptability and flexibility skills can embrace new technologies, quickly learn how to operate advanced machinery,, and leverage digital tools to improve efficiency and productivity.
- Responding to Market Changes: The manufacturing industry is influenced by ever-changing market demands and customer preferences. Adaptability and flexibility skills enable organizations to pivot and respond to market trends, modify production processes, and develop new products or services that cater to evolving customer needs.
- Embracing Process Improvements: In an era of continuous improvement, organizations must foster a culture of adaptability and flexibility skills to drive process enhancements.
- Enhancing Problem-Solving Abilities: Adaptability and flexibility skills enable employees to navigate unexpected challenges and find innovative solutions effectively. Employees can approach problems with resilience and creativity by fostering a flexible mindset.
Growth Market
According to Forbes, organizations prioritizing adaptability and flexibility in their workforce have a higher chance of success in the long run.
In addition, McKinsey & Company's research arm has identified adaptability and continuous learning as crucial skills for businesses to remain competitive and achieve market growth.
5. Leadership and Teamwork Skills
Effective leadership and teamwork skills create a positive work environment, drive productivity, and cultivate a culture of innovation. By providing training programs focusing on leadership development and promoting strong teamwork, your organization can unlock the potential for enhanced collaboration, employee engagement, and overall business success.
Role of leadership and teamwork skills in driving successful manufacturing operations
- Setting a Clear Vision: Strong leadership and teamwork skills in manufacturing establish a clear vision that aligns with the organization's goals. Leaders inspire employees to work towards common objectives and foster a sense of purpose and direction.
- Facilitating Effective Communication: Leadership and teamwork skills are vital as they ensure that information flows smoothly between different teams, departments, and stakeholders, fostering collaboration and problem-solving.
- Providing Guidance and Support: Effective leadership and teamwork skills provide guidance and support to their teams, helping employees overcome challenges, develop their skills, and reach their full potential. They create a nurturing environment that encourages growth, learning, and continuous improvement.
Developing strong leaders who inspire, guide, and empower their teams fosters a positive work environment that drives productivity and innovation. Encouraging teamwork and collaboration enhances problem-solving capabilities, stimulates creativity, and improves operational efficiency.
Growth Market
According to a report by Deloitte, leadership and teamwork skills are critical manufacturing skills that have contributed significantly to job market growth in the industry. In addition, the report states that high innovators in the manufacturing sector prioritize the development of these skills to achieve success.
6. Quality Control and Assurance Skills
Quality control and assurance skills ensure that products meet customer expectations, minimize defects, and enhance overall business reputation. By investing in training programs focusing on quality control and assurance, your organization can upskill employees and drive business growth by delivering superior products and services.
Learn more: Quality Control and Assurance Training
Benefits of Investing in Quality Control and Assurance Skills:
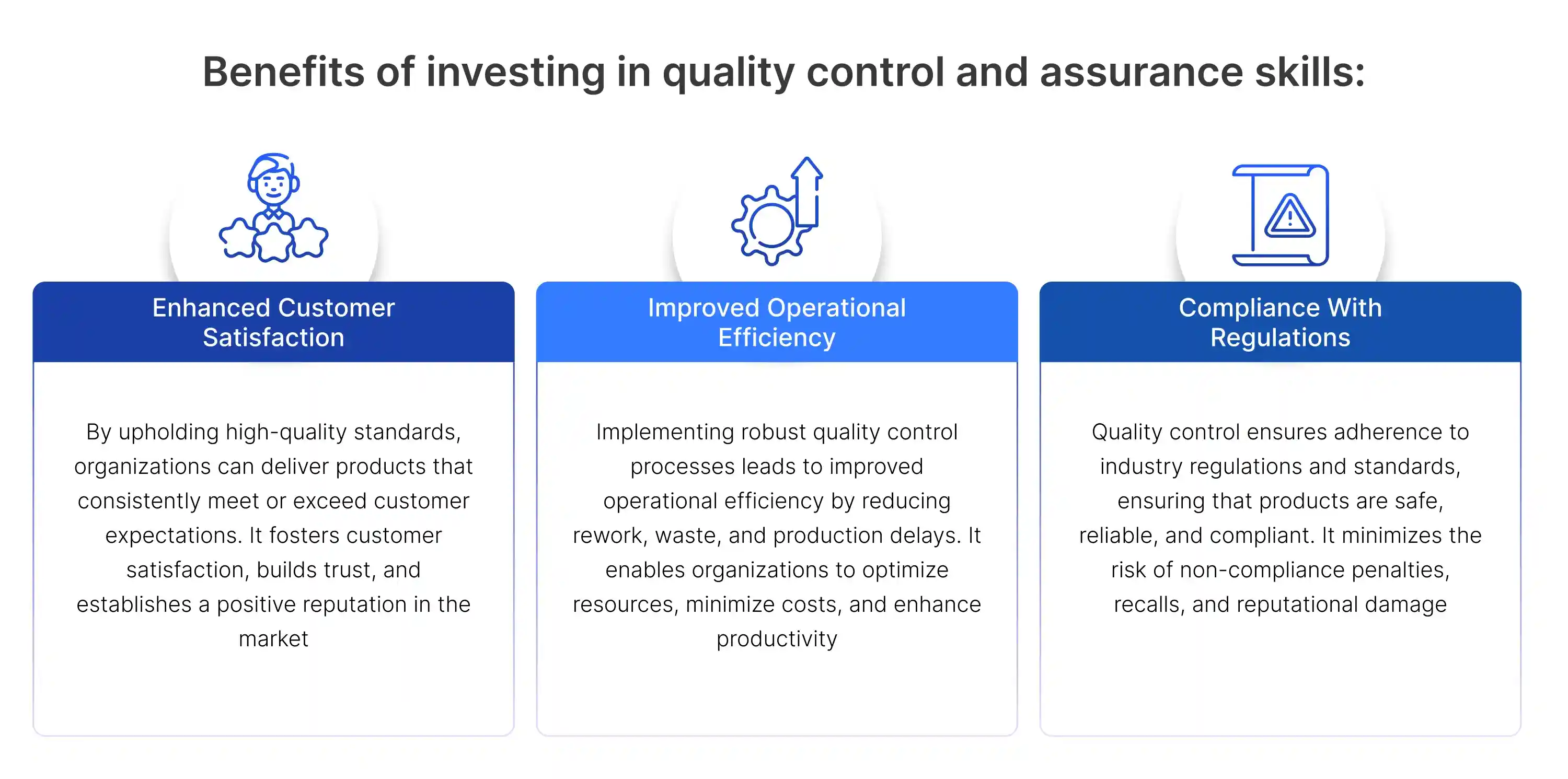
Emphasizing the importance of quality control and assurance skills and implementing targeted training programs will enable your organization to foster a manufacturing quality culture, driving business growth and success in today's competitive market.
7. Continuous Improvement and Lean Manufacturing Skills
Continuous Improvement and Lean Manufacturing Skills empower employees to identify and implement initiatives that optimize processes, eliminate waste, and drive efficiency. By investing in training programs focusing on continuous improvement, your organization can upskill employees and unlock the potential for business growth and success.
Skills Needed to Identify and Implement Continuous Improvement Initiatives:
8. Time Management and Efficiency Skills
Time management and efficiency skills equip employees with the techniques and strategies to optimize their productivity, reduce waste, and make the most of their time. By investing in training programs focusing on time management and efficiency skills, your organization can upskill employees and unlock the potential for increased productivity, improved performance, and, ultimately, business growth..
Prioritizing time management and efficiency through training programs demonstrates your organization's commitment to productivity and growth, empowering professionals to reach their full potential and drive the success of your business.
9. Health and Safety Knowledge Skills
The health and safety knowledge for a safe working environment skills equips employees with the necessary skills to ensure a safe workplace, minimize risks, and foster a culture of well-being.
Benefits of Investing in Health and Safety Knowledge for a Safe Working Environment Skills:
10. Analytical and Data Interpretation Skills
Analytical and data interpretation skills equip employees with the ability to extract insights, make informed decisions, and drive business growth. By investing in training programs focusing on analytical and data interpretation skills, your organization can upskill employees and unlock the potential in manufacturing decision-making, improved operational efficiency, and, ultimately, business growth.
Importance of Analytical and Data Interpretation Skills in Manufacturing Industry:
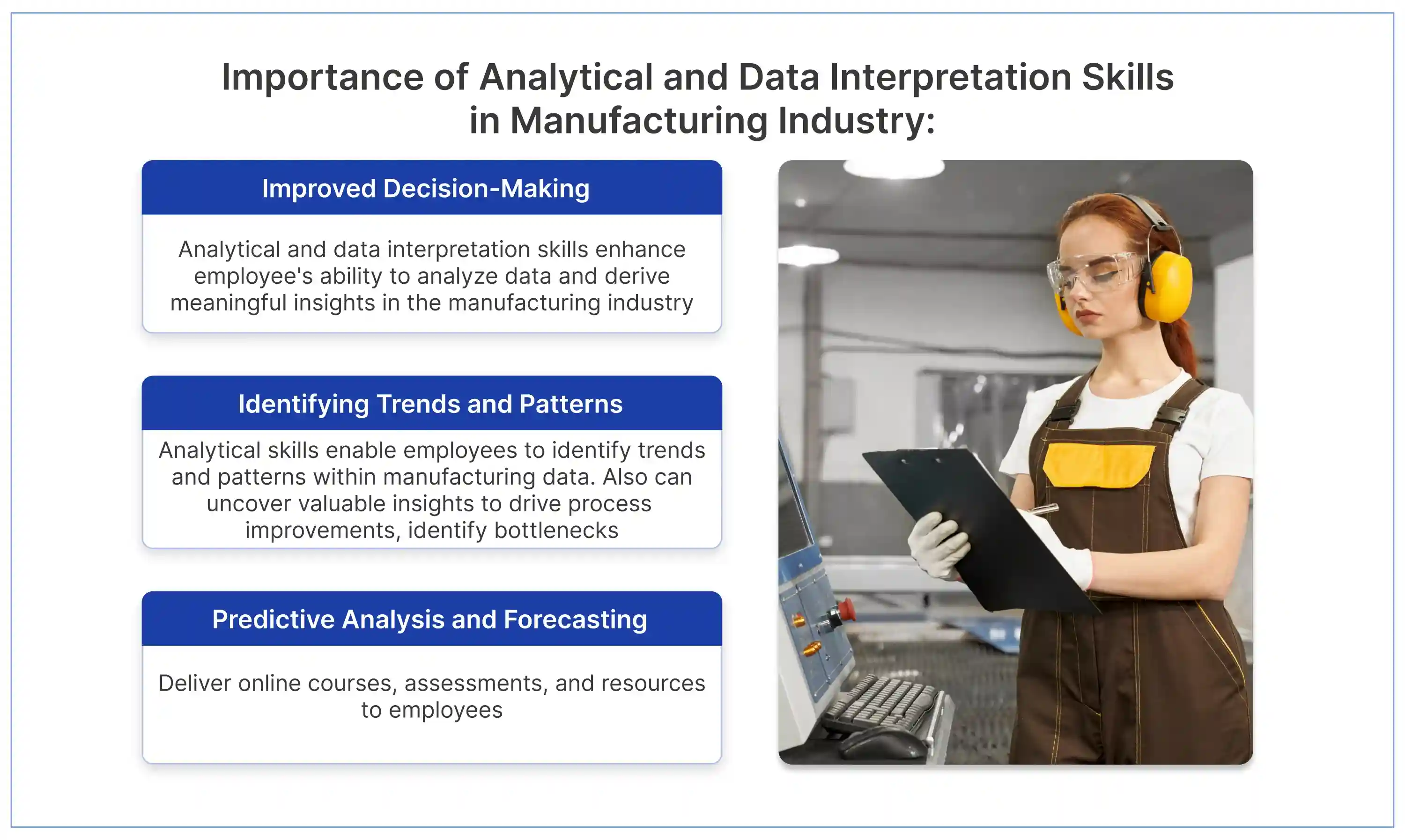
Conclusion
Investing in training programs to upskill employees in the 10 most in-demand skills in manufacturing is a strategic move that can fuel your organization's growth and success. Empowering your workforce with these essential skills can enhance operational efficiency, drive innovation, and stay ahead in a competitive market. Embrace the power of training program and unlock the full potential of your employees to propel your business to new heights of success.
Explore High-impact instructor-led training for your teams.
#On-site #Virtual #GroupTraining #Customized
Edstellar Training Catalog
Explore 2000+ industry ready instructor-led training programs.
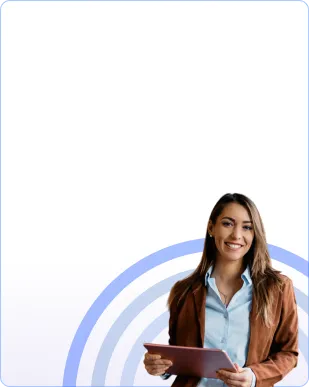
Coaching that Unlocks Potential
Create dynamic leaders and cohesive teams. Learn more now!
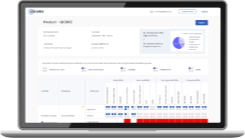
Want to evaluate your team’s skill gaps?
Do a quick Skill gap analysis with Edstellar’s Free Skill Matrix tool
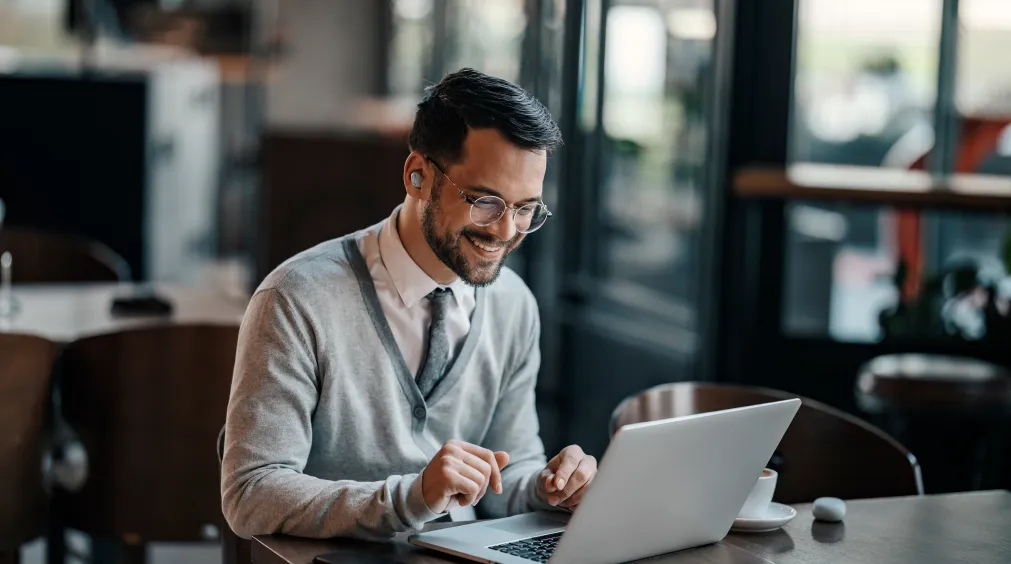
Stay informed on L&D best practices
Get periodic updates on learning and development industry trends, expert insights, success stories and innovative training practices from Edstellar.
Featured Post
.webp)
Contact Us
Submit your Training Requirements below and We'll get in touch with you shortly.