Ever feel like your business is running in circles constantly busy, yet not making real progress? That’s often the result of inefficient processes. Companies that don’t take the time to streamline their operations end up dealing with higher costs, wasted resources, and missed opportunities. According to McKinsey & Company, organizations that implement process optimization strategies can increase their output by 25% within a year all without additional capital investment.
The question is, how can businesses achieve this level of efficiency? The answer lies in structured problem-solving methodologies, with DMAIC one of the most widely used Lean Six Sigma approaches emerging as a key framework for process improvement.
Rooted in the Lean and Six Sigma quality improvement frameworks, DMAIC stands for Define, Measure, Analyze, Improve, and Control. It was developed in the 1950s through the pioneering work of W. Edwards Deming and has been a go-to methodology for Six Sigma professionals for decades. More than just a problem-solving tool, it is a structured, data-driven methodology designed to help businesses pinpoint inefficiencies, eliminate defects, and drive measurable improvements.
By following its five-phase approach, organizations gain a systematic roadmap for not only optimizing workflows but also fostering a culture of continuous improvement and operational excellence.
In this article, we'll delve into the DMAIC process, exploring each phase in detail and demonstrating how it serves as a powerful tool for process enhancement and effective problem-solving.
What is DMAIC Process - The 5 Phases Explained
As previously mentioned, the DMAIC methodology has its roots in the Six Sigma quality improvement process. Developed in the 1980s by engineers at Motorola, including Bill Smith, Six Sigma was created as a response to the company's need to catch up with Japanese competitors in quality and efficiency. The goal was to systematically reduce defects and variability in manufacturing processes, leading to the formulation of a structured problem-solving approach.
While Six Sigma focused on reducing defects, Lean principles were integrated to eliminate waste and enhance process flow, making DMAIC a powerful tool for both quality and efficiency improvements. This approach initially encompassed four stages: Measure, Analyze, Improve, and Control (MAIC). Later, the 'Define' phase was added, evolving into what we now know as DMAIC.
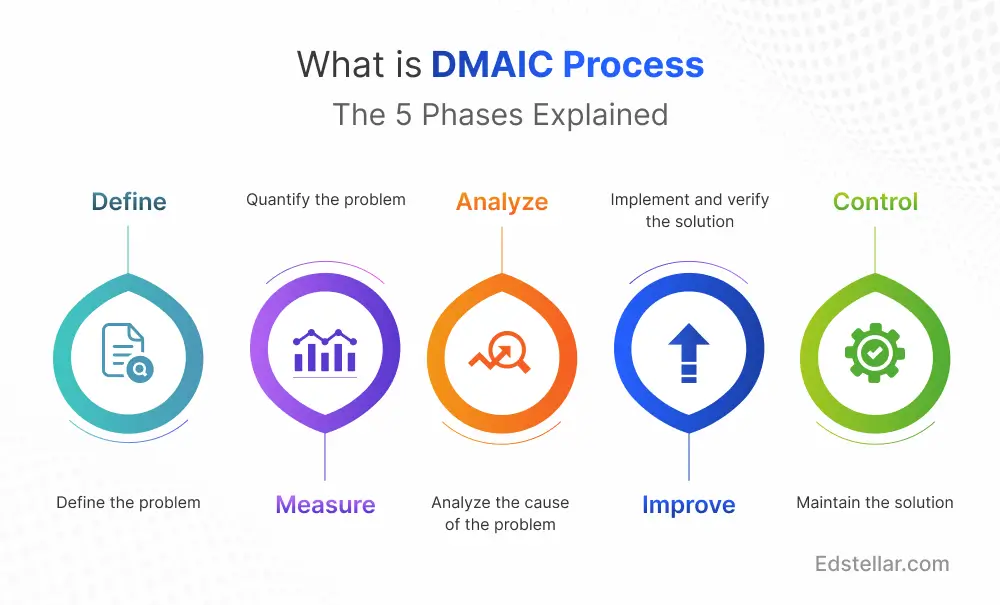
In a world where businesses must constantly adapt and refine their processes, the need for structured problem-solving remains vital. DMAIC provides a systematic approach to identifying inefficiencies, solving root causes, and driving continuous improvement making it a key tool for sustainable success.
- Define: This phase sets the foundation for effective process improvement or problem-solving. The team collaborates to clearly identify what needs to be improved, assess the current state, define the desired outcome, and establish the purpose behind the initiative. A well-defined problem statement prevents wasted efforts, and provides a clear direction for the entire improvement process.
- Measure: In this phase, the team delves deep into the problem, ensuring a comprehensive understanding of its scope. The first step is to identify and measure key performance metrics that establish a baseline for comparison. Beyond just metrics, the team also examines influencing factors that may be contributing to inefficiencies, ensuring no critical variables are overlooked.
- Analyze: In this phase, the team leverages data to thoroughly diagnose the problem and pinpoint its root causes. They delve deeper into patterns, bottlenecks, and contributing factors to uncover the true sources of inefficiencies. This phase also helps establish cause-and-effect relationships, ensuring that solutions directly address the core issues rather than just the symptoms.
- Improve: This is the phase where solutions are developed, implemented, and tested to drive meaningful change. The team refines processes, introduces innovations, and applies strategic adjustments to eliminate root causes. Whether through workflow enhancements, automation, or operational changes, every solution is designed to create measurable improvements in efficiency and effectiveness. Testing and validation play a crucial role in this phase, ensuring that changes deliver the desired impact before full-scale adoption.
- Control: After implementation, this phase ensures that improvements deliver sustained results. The team establishes monitoring systems, standard operating procedures (SOPs), and control measures to keep processes performing at the required level. By tracking key metrics and addressing deviations proactively, they prevent regression and reinforce long-term efficiency, ensuring continuous progress rather than one-time fixes.
How to Implement DMAIC Methodology in Your Organization: A Step-by-step Process
.webp)
Phase 1: Define - Identifying the Problem and Setting the Plan for Process Improvement
Step 1 - Define the Problem
The first step is to identify key stakeholders and clearly define the issue that needs resolution. This involves gathering input from relevant departments, collecting preliminary data, and reviewing customer feedback to ensure a thorough understanding of the problem. The problem statement should be specific, measurable, and aligned with business goals to provide a strong foundation for the improvement process.
Step 2 - Establish the Project Scope
Once the problem is clearly defined, the team establishes the project scope to maintain focus and prevent scope creep. At this stage, stakeholders are formally engaged to ensure alignment and gather their input on process boundaries. Using SIPOC (Suppliers, Inputs, Process, Outputs, Customers) mapping, the team outlines the entire process, defines responsibilities, and ensures that all involved parties understand their roles in the improvement initiative.
Step 3 - Assemble the Right Team
With the problem clearly defined and the project scope established, the next step is to form a cross-functional team that will drive the improvement initiative. The team should include process owners, analysts, Six Sigma experts, and key stakeholders identified in Step 1 to ensure a well-rounded approach.
Diverse representation is crucial as it brings different perspectives, fosters collaboration, and ensures that decisions are both data-driven and practical for execution. Roles and responsibilities are assigned based on expertise, and leadership formally approves resource allocation and commitment to the project.
Step 4 - Develop a Project Charter
With the problem defined, project scope established, and team assembled, the next step is to formalize the initiative through a Project Charter. This document serves as the official authorization for the project, outlining the problem statement, objectives, success criteria, timeline, and key stakeholders. It ensures clarity in roles, responsibilities, and expected outcomes, aligning all involved parties on a shared vision.
Securing leadership approval at this stage is essential to ensure resource allocation, priority alignment, and commitment from stakeholders, enabling a smooth execution of the project.
Phase 2: Measure - Collecting and Validating Data for Process Optimization
Step 1 - Identify KPIs
To measure process performance effectively, the team establishes clear, quantifiable KPIs aligned with project goals. These metrics serve as a baseline for comparison, ensuring progress is tracked accurately. Selecting the right KPIs is crucial irrelevant or misleading metrics can distort analysis and lead to ineffective solutions. Each KPI should be specific, measurable, and directly tied to the project objectives, providing actionable insights for informed decision-making.
Step 2 - Develop a Data Collection Plan
With KPIs defined, the next step is to create a structured data collection plan that outlines what data will be collected, how frequently, and through which methods. A standardized approach is essential to maintaining data integrity and reliability, since inconsistent or poorly defined data collection methods can lead to inaccurate insights. By ensuring consistency in measurement, the team can generate accurate insights that drive effective process improvements.
Step 3 - Gather Baseline Data
To establish a reliable benchmark for comparison, the team collects historical and real-time data to assess current process performance. By analyzing data trends over time rather than relying on a single snapshot, the team ensures a more accurate and comprehensive understanding of process variations and inefficiencies. A well-defined baseline serves as a reference point for measuring the impact of future improvements.
Step 4 - Validate and Review Data
Before proceeding, the team conducts a Measurement System Analysis (MSA) to verify data accuracy, consistency, and reliability. This step is critical in ensuring that decisions are based on valid insights rather than flawed data. Inaccurate or inconsistent data can mislead analysis and compromise the entire project direction, making thorough validation essential for meaningful improvements.
Phase 3: Analyze - Identifying Root Causes of Problems in Processes
Step 1 - Conduct Root Cause Analysis (RCA)
Using techniques such as Fishbone Diagrams, 5 Whys, and Pareto Analysis, the team systematically identifies the underlying causes of process inefficiencies. The focus is on eliminating root causes rather than addressing surface-level symptoms, as temporary fixes can lead to recurring issues. A thorough RCA ensures that improvements are targeted, sustainable, and effectively resolve the core problem.
Step 2: Assess Process Variability
After identifying root causes, the next step is to analyze process variability to understand how fluctuations impact performance. Using statistical analysis, the team evaluates trends, inconsistencies, and deviations that may be contributing to inefficiencies. Comparing historical data with current performance helps identify recurring patterns and potential disruptions. Addressing these variations ensures that improvements are not only effective but also sustainable in the long run.
Step 3: Prioritize Issues for Resolution
With root causes identified and process variability assessed, the team now ranks issues based on their impact, feasibility, and overall business value. Not all problems can be tackled simultaneously, so prioritization ensures that efforts are directed toward the most critical inefficiencies first. By focusing on high-impact, achievable improvements, the team maximizes resource efficiency and ensures that solutions deliver measurable benefits.
Phase 4: Improve - Developing, Testing and Scaling Process Improvement Solutions
Step 1: Brainstorm Potential Solutions
With high-priority issues identified, the team now collaborates to generate potential solutions through brainstorming, benchmarking, and expert consultations. Each idea is evaluated based on feasibility, impact, and scalability to ensure practical implementation. While innovation is encouraged, solutions must be realistic, actionable, and aligned with business objectives to drive sustainable improvements.
Step 2: Develop a Pilot Implementation Plan
After identifying feasible solutions, the team designs a structured pilot implementation plan to test proposed improvements on a smaller scale before a full rollout. This controlled approach allows for real-time evaluation, helping to identify potential challenges and refine the solution as needed. Pilot testing is essential to mitigate risks, ensuring that the changes deliver measurable improvements before committing significant resources to full-scale execution.
Step 3: Execute and Monitor Pilot Runs
With the pilot plan in place, the team implements the proposed changes in a controlled environment to assess their real-world impact. Throughout the pilot phase, data is continuously collected and analyzed to measure performance improvements and identify any unintended consequences. Real-time monitoring is crucial at this stage, allowing the team to make adjustments before moving to full-scale implementation, ensuring the solution is both effective and sustainable.
Step 4: Full-Scale Implementation
After validating the pilot results, the team proceeds with a structured rollout of the solution across the organization. A phased implementation strategy is often used to minimize disruption, address potential challenges incrementally, and enhance user adoption. Clear communication, training, and stakeholder engagement play a crucial role in ensuring a smooth transition and widespread acceptance of the changes. Gradual deployment helps mitigate resistance and allows for course correction if needed.
Phase 5: Control - Standardizing Practices, Monitoring and Driving Continuous Improvement
Step 1: Establish Monitoring Mechanisms
With the full-scale implementation complete, the focus shifts to the Control Phase, sustaining process improvements through continuous monitoring. The team implements dashboards, control charts, and performance tracking tools to measure ongoing effectiveness and quickly identify deviations. Proactive tracking is essential to prevent regression and ensure that improvements remain aligned with business objectives. Regular performance reviews help in making data-driven adjustments, reinforcing long-term success.
Step 2: Standardize Best Practices
As part of the Control Phase, the team documents Standard Operating Procedures (SOPs) and work instructions to ensure consistency in process execution. Clear and accessible documentation is essential for maintaining adherence and preventing deviations. Overly complex SOPs can lead to non-compliance, so the focus should be on creating structured, user-friendly guidelines that enable smooth implementation and long-term sustainability.
Step 3: Conduct Training and Knowledge Transfer
To ensure the long-term success of standardized processes, the team conducts training sessions and knowledge-sharing workshops to familiarize employees with the new workflows. Practical, engaging training is crucial for smooth adoption, reinforcing best practices, and minimizing resistance to change. Employee buy-in is essential ensuring they understand the value of these improvements increases compliance and long-term adherence.
Step 4: Schedule Periodic Audits and Reviews
The final step in the Control Phase is to establish a system for ongoing evaluation through scheduled audits and governance reviews. These reviews help identify gaps, inefficiencies, and opportunities for further improvement, ensuring that processes remain optimized over time. Embedding continuous improvement into the company culture ensures that changes are sustained, keeping efficiency and effectiveness at the forefront of operations.
Common Pitfalls in the Implementation of DMAIC and How To Avoid Them
While DMAIC is a powerful framework for driving process improvement, organizations often stumble into common pitfalls that undermine its effectiveness. Avoiding these missteps can make the difference between a successful project and one that misses its mark. Here's a breakdown of frequent mistakes and how to steer clear of them:
Neglecting to Collect Enough Data
One of the biggest mistakes is failing to gather sufficient data to fully understand the problem. While cost and time savings often take center stage, there are other valuable outcomes like improved employee satisfaction, enhanced safety, and better quality that shouldn't be overlooked. Even if these benefits don’t directly result in monetary gains, they can positively impact the organization’s culture and overall performance.
How to Avoid It: Ensure you measure these intangible benefits upfront so that their improvements can be verified after implementation. A comprehensive data collection plan is key to driving informed decisions.
Solely Relying on Documentation
Improvement efforts often fail when they focus only on documented processes or policies without addressing what’s actually happening on the ground. If gaps between standard procedures and real-life practices aren’t identified, changes won’t address the root causes of inefficiencies.
How to Avoid It: During the Define and Measure phases, observe real workflows and uncover deviations caused by training deficits or outdated processes. Align your efforts with what’s happening, not just what’s written.
Blaming Employees Instead of Processes
Mistakes are often attributed to employees, but in reality, they’re usually the result of poor system design or insufficient training. Most employees want to perform well, but their success depends on the structure and tools provided to them.
How to Avoid It: Focus on identifying flaws in the process rather than pointing fingers. Create an environment where employees feel empowered to share feedback and suggest improvements, fostering a culture of continuous improvement.
Relying Solely on Leadership
Another common mistake is placing the responsibility for identifying and solving problems solely on leadership. While leaders play a critical role, employees closest to the work often have the best insights into inefficiencies and potential solutions.
How to Avoid It: Form cross-functional teams that involve employees at all levels of the organization. This approach encourages collaboration, creativity, and buy-in, resulting in better solutions that address the real issues.
Skipping Continuous Improvement Tools
Failing to leverage continuous improvement software can lead to missed opportunities for tracking, measuring, and sustaining improvements. Without the right tools, it’s easy for ideas and progress to get lost.
How to Avoid It: Invest in continuous improvement software to capture ideas, measure the impact of changes, and facilitate communication between employees and leadership. These tools improve accountability, enable real-time data analysis, and ensure long-term success for your DMAIC projects.
Case Study: Application of DMAIC in an Industrial Setting
This case study explores the implementation of DMAIC at Fehst Componentes, Lda, Portugal, a company specializing in plastic interior decorative components for the automotive industry.
The company faced a high percentage of non-conforming parts in an injection-molded component called High Gloss Blend. The main challenge was to reduce defects occurring after the painting process, which led to a significant increase in costs and reduced customer satisfaction.
DMAIC Implementation
1. Define Phase:
- The project began by analyzing historical production data from April to September 2019.
- The component with the highest defect rate was identified: High Gloss Blend.
- The acceptable defect percentage set by the company was 22%, but actual defect rates exceeded 47.6% in September 2019.
- The main objective was to reduce the percentage of non-conforming parts and enhance the manufacturing process.
2. Measure Phase:
A visual inspection system using sensors was employed to detect defects.
The system identified two primary defects:
- Inclusions (protrusions on the surface after painting)
- Pits (small depressions)
A Pareto analysis showed that inclusions were the most critical defect requiring immediate attention.
3. Analyze Phase:
A brainstorming session involving process engineers and quality teams was conducted.
Ishikawa (Fishbone) Diagram and 5 Whys Analysis were used to determine root causes:
- Static electricity on plastic parts attracted impurities before painting.
- Handling and packaging contributed to defects.
- Ineffective CO₂ cleaning system before painting led to contamination.
- Gloves used by workers affected the surface quality of parts.
4. Improve Phase:
Based on the findings, several improvements were implemented:
- Handling & Gloves:
- Workers started using white cloth gloves instead of nitrile gloves to reduce contamination.
- Cloth gloves helped in early detection of dirt, prompting frequent changes.
- Ionization & Packaging:
- An ionization system was added before the painting stage to remove static electricity.
- Traditional plastic packaging was replaced with anti-static bags, which led to a 40% reduction in defects.
- CO₂ Cleaning System Enhancement:
- The CO₂ cleaning system lost efficiency over time, leading to inconsistent cleaning.
- A cryogenic CO₂ tank with a steady gas flow was installed, ensuring uniform cleaning and reducing non-conformities by an additional 5.75%.
5. Control Phase:
- The improvements were tested through statistical monitoring and control charts.
- By December 2019, the defect rate had fallen below the acceptable threshold of 22%.
- Continuous employee training and standard operating procedures (SOPs) were established to sustain improvements.
Outcome: The application of the DMAIC methodology at Fehst Componentes, Lda. led to a substantial reduction in defects, lowering the rate from 47.6% to below 22%. This improvement enhanced product quality and increased customer satisfaction. Additionally, by addressing the root causes of defects, the company streamlined its processes, improving overall efficiency and reducing other manufacturing inconsistencies.
This case study highlights how a structured approach like DMAIC can drive sustainable quality improvements. Moving forward, the company could benefit from fully integrating Six Sigma to eliminate inefficiencies and implement advanced technological solutions for further process optimization.
Conclusion: What Lies Ahead In DMAIC
DMAIC has long been a cornerstone of Six Sigma methodologies, offering a structured approach to process improvement. Looking ahead, its adaptability positions it well to integrate with emerging trends in process optimization. For instance, the rise of Digital Adoption Platforms (DAPs) is enhancing user training and software utilization, thereby accelerating proficiency and reducing support costs.
Additionally, the integration of Robotic Process Automation (RPA) is streamlining repetitive tasks, allowing organizations to focus on more strategic initiatives.
By embracing these advancements, DMAIC can continue to drive efficiency and quality improvements in the evolving business landscape.
Explore High-impact instructor-led training for your teams.
#On-site #Virtual #GroupTraining #Customized
Edstellar Training Catalog
Explore 2000+ industry ready instructor-led training programs.
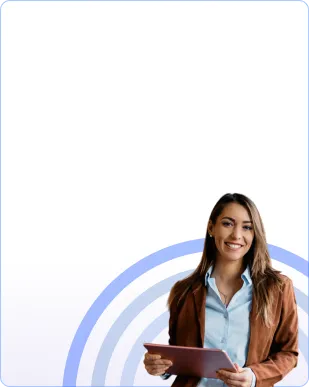
Coaching that Unlocks Potential
Create dynamic leaders and cohesive teams. Learn more now!
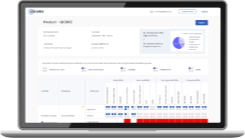
Want to evaluate your team’s skill gaps?
Do a quick Skill gap analysis with Edstellar’s Free Skill Matrix tool
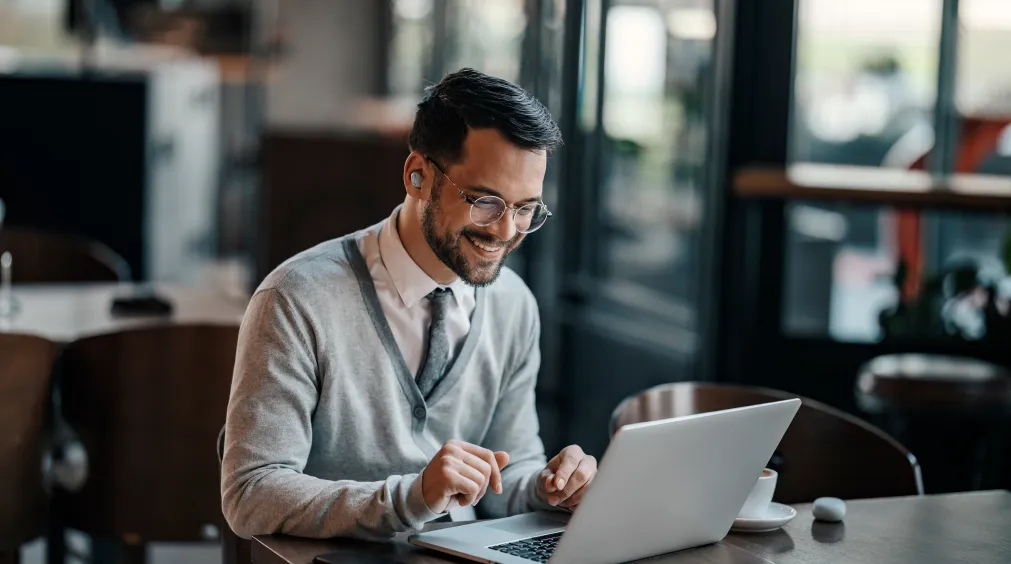
Stay informed on L&D best practices
Get periodic updates on learning and development industry trends, expert insights, success stories and innovative training practices from Edstellar.
Featured Post
.webp)
Contact Us
Submit your Training Requirements below and We'll get in touch with you shortly.