In the early 1980s, Western business leaders found themselves grappling with a pressing question: how were Japanese manufacturers consistently surpassing them in both quality and cost? Fast forward to 2025, and Total Quality Management (TQM) has evolved from being just another business methodology to becoming the backbone of successful enterprises worldwide. But, while many organizations claim to practice TQM, few truly understand its transformative power in today's digital-first business environment.
TQM is your organization's quality compass – it does not just catch defects or maintain standards. It creates a culture where every team member, from the C-suite to the production floor, is invested in delivering excellence. In an era where one negative customer review can go viral, and supply chain hiccups can cause ripple effects across continents, TQM isn't just nice to have – it's essential for survival.
Research indicates that TQM affects 71.7% of productive behavior making it a revolutionary approach to quality management that would transform the global business landscape forever.
In this blog, we'll explore how modern businesses are reinventing TQM principles for the digital age and why getting it right could be the competitive edge your organization needs. Whether you're a manufacturing veteran or a tech startup, understanding TQM's evolution from its Japanese manufacturing roots to today's agile business environment could be the game-changer you've been looking for.
Key Principles of Total Quality Management (TQM)
At its core, TQM is about one thing: continuous improvement. It's an approach that focuses on enhancing the quality of everything your organization produces – whether that's physical products or services. But here's the interesting part: it's not just about the end product. TQM is equally concerned with improving all your internal processes along the way.
The Fascinating History
The story of TQM shows how long businesses have been thinking about quality management. It all started in the early 1900s with Walter A. Shewhart, who's often called the father of modern quality control. His 1931 work, "Economic Control of Quality of Manufactured Product," laid the groundwork for how we think about manufacturing quality control today.
The plot thickens in the 1950s when Joseph M. Juran enters the picture. After spending time in Japan, he wrote "What Is Total Quality Control? The Japanese Way" in 1954. Juran's experience working with Japanese scientists and engineers gave him unique insights that he later shared in "Quality Planning and Analysis."
Juran’s work, along with contributions from other quality pioneers, laid the foundation for what would become Total Quality Management (TQM). His principles emphasized a systematic approach to quality, influencing businesses worldwide. These ideas evolved into core TQM principles that organizations continue to follow today.
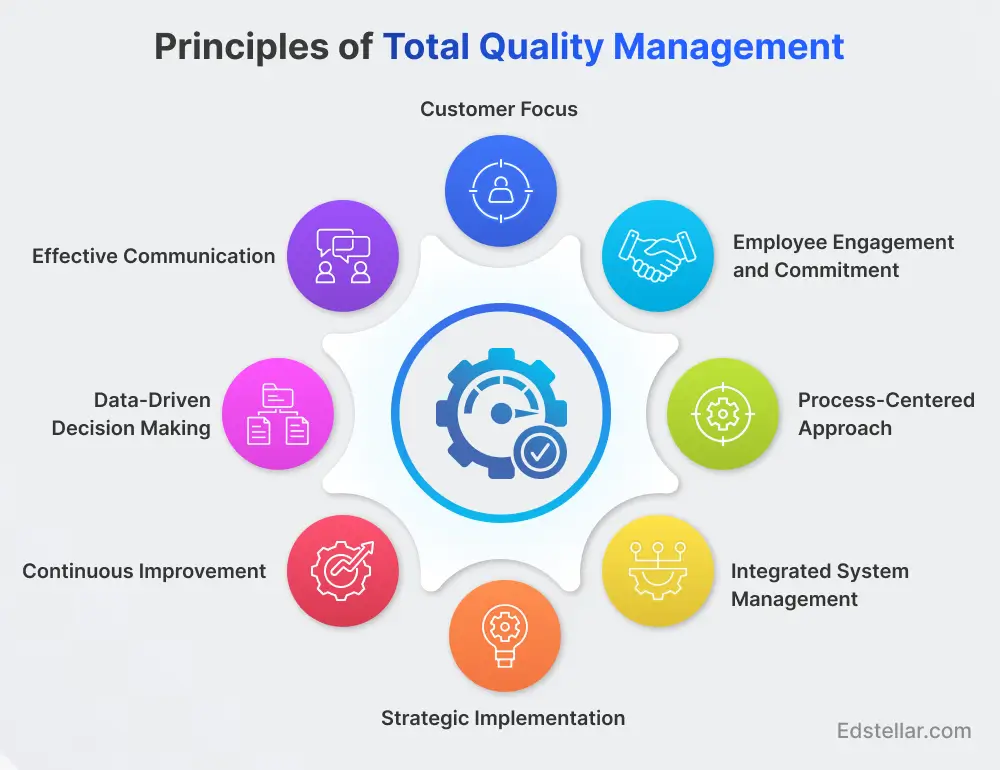
1. Customer Focus
Quality is fundamentally determined by customer satisfaction and market response. Businesses that prioritize superior customer service can experience revenue growth between 4% and 8% above their market average. Organizations must:
- Research and understand customer needs and expectations systematically
- Align organizational objectives with customer requirements
- Establish robust feedback mechanisms and satisfaction metrics
- Manage customer relationships strategically
- Balance stakeholder interests (customers, employees, suppliers, investors)
Benefits: Enhanced market share, increased revenue, stronger customer loyalty, and positive word-of-mouth marketing.
2. Employee Engagement and Commitment
Success depends on organization-wide participation and dedication. Companies with highly engaged employees are 21% more profitable than those with low engagement levels. Implementation requires:
- Clear communication of organizational vision and objectives
- Development of ownership and problem-solving capabilities
- Implementation of self-evaluation mechanisms against personal goals
- Recognition of performance excellence
- Provision of comprehensive training and resources
- Creation of an environment fostering open discussion and innovation
Benefits: Improved retention, increased innovation, enhanced accountability, and sustained continuous improvement culture.
3. Process-Centered Approach
Systematic process management is essential for quality consistency. Key elements include:
- Development of detailed process flowcharts and visual action plans
- Clear delineation of roles and responsibilities
- Regular analysis of process efficiency and bottlenecks
- Assessment of process impact on stakeholders
- Integration of quality controls throughout the workflow
Benefits: Accelerated production cycles, reduced costs, consistent outcomes, and focused improvement opportunities.
4. Integrated System Management
Quality management requires breaking down departmental silos through:
- Establishment of company-wide quality culture
- Visual representation of cross-functional processes
- Regular process improvement and optimization
- Comprehensive training programs
- Integration of horizontal processes across departments
Benefits: Enhanced organizational effectiveness, improved cross-functional coordination, and systematic quality improvement.
5. Strategic Implementation
Quality initiatives must align with organizational strategy through:
- Provision of appropriate training and resources
- Continuous process and equipment upgrades
- Integration of improvement metrics into performance objectives
- Recognition and reward of innovation
- Systematic deployment of quality initiatives
Benefits: Improved organizational capabilities, enhanced performance metrics, and strategic alignment of quality objectives.
6. Continuous Improvement
Organizations must maintain ongoing enhancement through... Utilizing Edstellar's training management platform, companies can continuously upskill their workforce, keeping them abreast of the latest quality management practices and tools, thereby embedding a culture of continuous improvement.:
- Establishment of measurable improvement goals
- Recognition of innovation and process enhancement
- Implementation of training and development programs
- Regular review and updating of standards
- Market adaptation capabilities
Benefits: Enhanced organizational capabilities, improved competitive position, and agile response to market changes.
7. Data-Driven Decision Making
Quality management requires systematic analysis through:
- Validation and verification of data accuracy
- Stakeholder access to relevant information
- Implementation of robust data collection methods
- Integration of factual analysis with experience
- Regular monitoring and reporting systems
Benefits: Enhanced decision-making capability, improved accountability, and data-supported strategic planning.
8. Effective Communication
Communication infrastructure must support quality initiatives through:
- Establishment of formal communication channels
- Employee involvement in decision-making processes
- Clear role definition and organizational alignment
- Regular updates on policy changes and procedures
- Cross-functional coordination mechanisms
Benefits: Improved morale, enhanced interdepartmental coordination, and increased employee motivation.
Ready to take your quality management efforts to the next level? Download the TQM Tracking Template now!
Case Studies of Successful TQM Implementation
Strategic TQM In North America’s Wind Energy Sector
Background: In the early 2020s, a mid-sized wind energy provider in North America faced significant challenges in its operations. The company was experiencing a decline in performance efficiency and quality issues, which were impacting its ability to maintain a competitive edge in the renewable energy market.
Challenges: The company encountered a 25% drop in turbine performance efficiency, a 15% increase in maintenance costs due to poor quality standards, and a 20% rise in customer complaints, primarily due to inconsistent service delivery. These operational inefficiencies and quality control problems were undermining the company’s reputation and profitability.
Solution: To resolve these challenges, the company initiated a strategic plan to implement a Total Quality Management (TQM) framework. This initiative aimed to standardize operations, improve efficiency, and enhance quality control across all levels of the organization.
Results and Outcomes: By adopting the TQM framework, the company was able to make its operations much smoother and improve service delivery. This led to a reduction in maintenance costs, better turbine performance, and a decrease in customer complaints. Ultimately, the company aligned its operations with industry best practices, securing a stronger position in the competitive renewable energy market.
AtlantiCare
Background: New Jersey-based healthcare provider AtlantiCare, with 5,000 employees across 25 locations, is a shining example of TQM in action.
Challenges: To enhance patient satisfaction, AtlantiCare identified communication gaps within their staff that were contributing to longer wait times and customer complaints. This issue required urgent attention to improve service delivery.
Solution: AtlantiCare implemented the 'Plan-Do-Check-Act' cycle as a framework to drive improvement. They focused on internal communication, ensuring the system fostered open, two-way feedback from day one. Performance excellence training was also introduced for new hires, emphasizing the importance of a quality-driven culture.
Results and Outcomes
This Strategy Yielded Significant Outcomes: AtlantiCare achieved its highest market share in six years, tripled repeat customer numbers and increased revenues from $280M to $650M. The organization's patient-first philosophy and commitment to continuous improvement helped it achieve leading success in the industry.
Santa Cruz Guitar Company
Background: Santa Cruz Guitar Company (SCGC), founded in 1976 by Luthier Richard Hoover, started as a small workshop in a basement. Over the years, it has evolved into a renowned artisan guitar manufacturer based in Santa Cruz, California.
Challenges: As the demand for SCGC guitars grew, the company faced challenges in maintaining the high standards of quality while increasing production. With a limited workforce of 14 expert craftsmen, the company had to balance custom orders with sustaining their commitment to excellence. Additionally, the substantial backlog of orders reflected the overwhelming demand, presenting a challenge in managing customer expectations and timely delivery.
Solution: To address these challenges, SCGC maintained a highly structured production process. The workshop is divided into six workstations, each overseen by a senior craftsman. Guitars are assembled in stages, moving from one station to the next. Owner Richard Hoover stays actively involved in all phases of construction and personally handles customer relations.
Results and Outcomes: Despite the growing demand, SCGC has managed to maintain a production of over 800 guitars annually, preserving the exclusivity and quality of their instruments. The company's continued focus on craftsmanship and limited production has allowed it to uphold its reputation for producing exceptional guitars with unique character.
Challenges in TQM Implementation
Effective TQM implementation requires continuous learning and experience building throughout the organization. Companies must constantly upgrade their understanding of both technical processes and evolving customer perceptions. Each challenge encountered should serve as a learning opportunity for organizational improvement.
Common Challenges in Total Quality Management Implementation
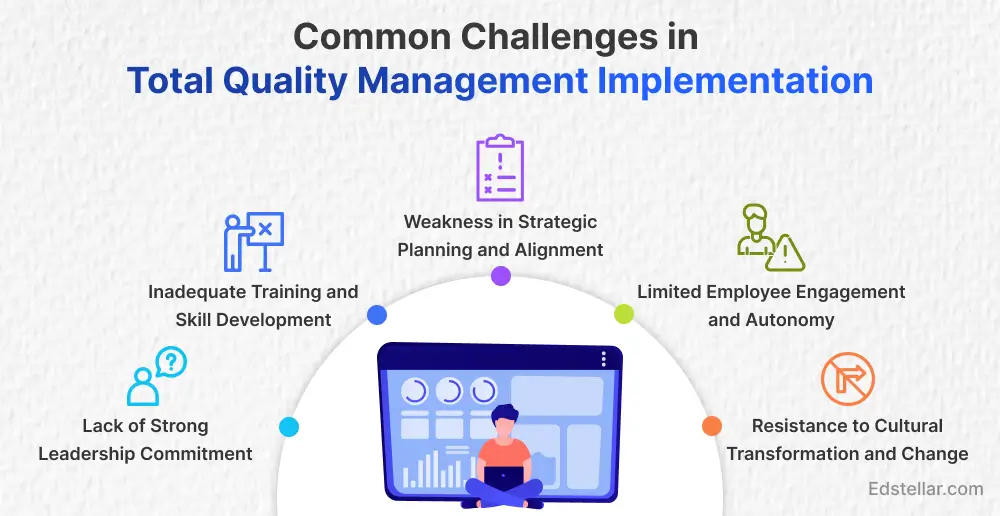
1. Lack of Strong Leadership Commitment
The cornerstone of successful TQM implementation lies in top management's dedication and involvement. When organizations delegate quality initiatives solely to external experts, it significantly diminishes the program's effectiveness. This lack of visible commitment cascades through organizational levels, ultimately affecting employee participation and engagement in quality initiatives.
2. Inadequate Training and Skill Development
Organizations often underestimate the fundamental importance of continuous training and education in TQM implementation. Without proper training, confusion regarding program aspects inevitably arises, compromising the entire quality structure. The effectiveness of TQM principles significantly increases when senior management actively participates in conducting training sessions.
3. Weakness in Strategic Planning and Alignment
Successful TQM implementation requires comprehensive planning involving all stakeholders across the organization. The focus should extend beyond immediate financial objectives to encompass broader organizational goals and quality improvements. Quality planning becomes ineffective when organizations fail to involve all relevant parties in the process.
4. Limited Employee Engagement and Autonomy
TQM success relies heavily on effective teamwork and employee empowerment at all levels. Organizations must recognize that collaborative work approaches require specific skill development and training. When employees lack proper empowerment to make process-related decisions, it leads to operational inefficiencies and workplace frustration.
5. Resistance to Cultural Transformation and Change
Organizational culture transformation represents one of the most challenging aspects of TQM implementation. The transition from traditional management approaches to a quality-focused culture typically requires several years of consistent effort. Organizations must understand that cultural change demands careful planning and effective communication to move from a fear-based to a trust-based environment.
The Future Of TQM
The evolution of Total Quality Management is driven by rising customer expectations for quality across all business interactions. As Amanda A. Russo, Operational Strategist at Cornerstone Paradigm Consulting, notes: "There is a balance in business; that balance is your people, their processes, technology, and your customer experience. We cannot focus on our customers if we don't address what we can control, which is our internal operations."
To stay competitive, organizations must adopt dynamic, data-driven strategies for quality management. Edstellar supports this shift by offering advanced tools for tracking performance metrics in real time, streamlining internal processes, and enabling continuous improvement. These solutions empower businesses to align operations with quality standards while staying focused on customer needs.
The future of TQM will require a holistic approach that balances customer focus with internal excellence and technological innovation. With Edstellar’s solutions, organizations can not only meet customer expectations but also drive long-term growth through improved quality management practices.
Explore High-impact instructor-led training for your teams.
#On-site #Virtual #GroupTraining #Customized
Edstellar Training Catalog
Explore 2000+ industry ready instructor-led training programs.
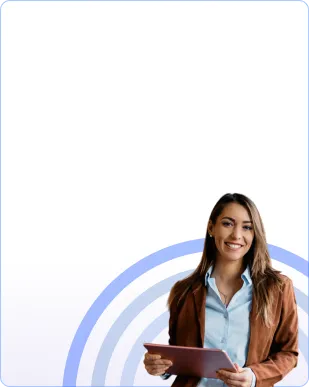
Coaching that Unlocks Potential
Create dynamic leaders and cohesive teams. Learn more now!
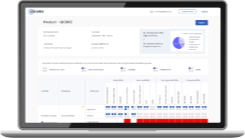
Want to evaluate your team’s skill gaps?
Do a quick Skill gap analysis with Edstellar’s Free Skill Matrix tool
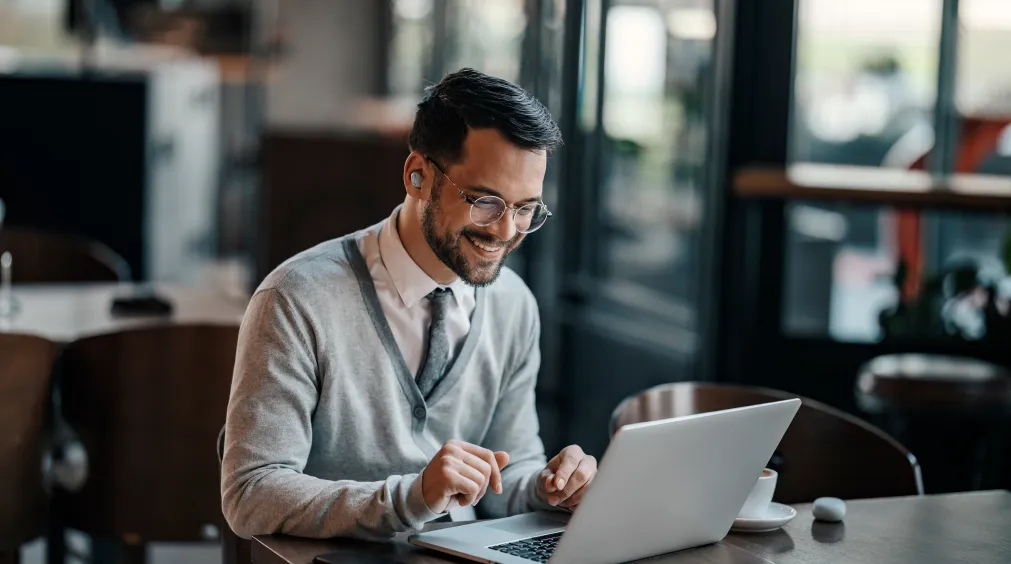
Stay informed on L&D best practices
Get periodic updates on learning and development industry trends, expert insights, success stories and innovative training practices from Edstellar.
Featured Post
.webp)
Contact Us
Submit your Training Requirements below and We'll get in touch with you shortly.