Every business leader knows the frustration: despite having top-tier talent, absolutely advanced technology and robust processes in place, something still holds your organization back from achieving its full potential. This is where the Theory of Constraints (TOC) comes in – a powerful management approach that's transforming how industry leaders view and solve their business challenges.
At its core, the Theory of Constraints operates on a remarkably straightforward principle: your organization's performance is invariably limited by a small number of constraints, much like a chain is only as strong as its weakest link. Whether it's a manufacturing bottleneck, a policy roadblock, or a market limitation, identifying and addressing these constraints can dramatically improve your entire system's performance.
Historically speaking, it was developed by Dr. Eliyahu Goldratt and introduced to the corporate world in his 1984 bestseller "The Goal”. In short words, the Theory of Constraints takes a scientific approach to business improvement. It's particularly relevant today as organizations face increasing pressure to optimize operations and maximize ROI.
The beauty of this methodology lies in its laser-focused approach: rather than trying to improve everything simultaneously, TOC helps you identify the one factor that's truly limiting your business growth - the bottleneck, as experts call it.
For senior leaders and decision-makers, understanding TOC isn't just about solving operational problems it's about gaining a strategic framework that can drive sustained business growth and competitive advantage. Let's explore how this powerful methodology can transform your organization's performance.
Understanding Constraints: The Basics
So first, what is a constraint? - A constraint is any resource whose capacity is less than or equal to demand for that resource or let’s say A constraint is a resource that can't handle more than or just meets the demand placed on it.
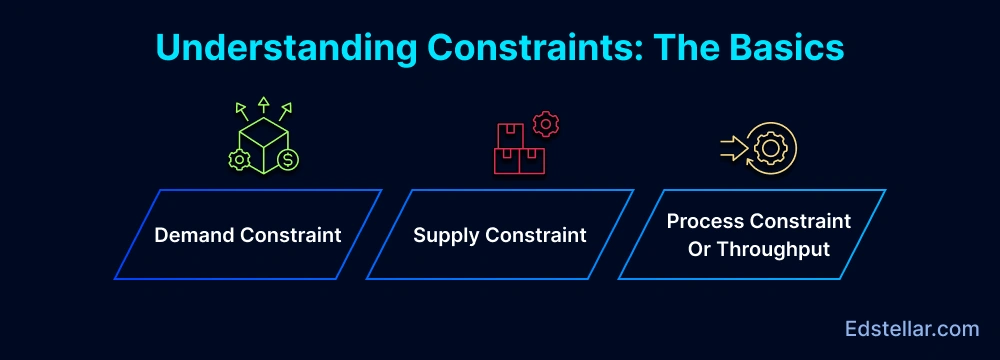
1. Demand Constraint
Taking example of the pandemic, when the pandemic initially started, the demand for masks went sky high to where companies couldn’t produce them fast enough to meet demand. The United Nations forecasted the demand for surgical masks alone to be in the region of 2.4 billion in 2020. Therefore, there was a demand constraint on the system.
2. Supply Constraint
Another example of a constraint is a supply constraint. During the pandemic, there was a significant shortage of semiconductor chips needed for manufacturing new cars. This bottleneck slowed production, preventing car manufacturers from meeting the rising demand for new vehicles. As a result, the value of used cars surged, transforming them into a highly sought-after commodity almost overnight.
3. Process Constraint or Throughput
This is the maximum amount achievable relative to output, very specific to production in this case. If a company can produce 100 units during an eight-hour workday, its throughput would be 100 units for that time period. A process constraint, in this case, refers to anything that hinders the company from reaching that production target. This leads us to the discussion of what the bottleneck is?
Delving into a Bottleneck
In the corporate landscape, bottlenecks are more than just slowdowns; they're capacity constraints that ripple through your entire operation. Picture an IT department receiving 100 service requests daily but only having the bandwidth to process 60. This capacity gap doesn't just affect the IT team – it cascades across departments, impacting productivity, employee satisfaction and ultimately, your bottom line.
Now to clear a common doubt, what is the difference between process constraints and bottlenecks. Let’s talk about those in detail before we step into the most important part of our blog.
.webp)
Step 1: Strategic Constraint Identification.
Identifying the true constraint in your process is often the most crucial step toward achieving your organizational goals. The success or failure of efforts to enhance efficiency or improve customer satisfaction can hinge on accurately pinpointing the weakest link in your system.
Step 2: Constraint Optimization
Take a deep dive into analyzing the constraint to fully understand its outputs and leverage them strategically. This approach allows you to uncover the root cause of your system's limitations and address them effectively, paving the way for lasting solutions.
Step 3: Process Synchronization
It's essential to synchronize your process capacity with that of the constraint to maximize system performance. This alignment ensures that the system supports the constraint's capabilities, preventing overproduction and enhancing overall efficiency.
Step 4: Performance Elevation
This phase typically requires significant resource allocation – whether that's capital for new equipment or budget for additional personnel. However, before making these investments, it's crucial to evaluate their potential impact through rigorous throughput accounting metrics to ensure they'll deliver the expected return on investment and genuinely improve your overall system performance.
Step 5: Continuous Improvement
This step emphasizes that the Five Focusing Steps should be applied as an ongoing improvement process, rather than as a one-time project.
How the Theory of Constraints Blends into Lean Manufacturing
Think of TOC and Lean as two powerful approaches to manufacturing excellence, each with its own unique focus. Theory of Constraints is like a spotlight operator in a theatre which constantly focuses on the single biggest limitation in your system – your constraint. Its primary goal is to maximize throughput by identifying and addressing these constraints, ultimately expanding your production capacity. On the other hand, Lean Manufacturing is more like a comprehensive cleaning crew, methodically working through your entire process to eliminate waste in all its forms, with the end goal of reducing operational costs.
While these methodologies might seem to pull in different directions – especially when it comes to inventory management and line balancing – they're actually quite complementary. TOC advocates for strategic inventory buffers around constraints and intentionally unbalanced lines to maximize throughput, whereas Lean pushes for minimal inventory and balanced lines to eliminate waste. The pacing also differs: TOC lets your constraint set the rhythm through Drum-Buffer-Rope, while Lean synchronizes to customer demand through Takt Time.
The Synergy Between Toc and Lean
At first glance, the Theory of Constraints (TOC) and Lean Manufacturing may appear to follow different paths. TOC focuses on improving one critical constraint at a time, while Lean aims to eliminate waste across the entire process. However, these methodologies aren’t contradictory they are complementary approaches that, when combined, can drive significant improvements in throughput, efficiency, and adaptability.
Together, they offer a powerful toolkit for solving business bottlenecks and improving processes in a way that maximizes both short-term gains and long-term sustainability. To truly understand how TOC and Lean work together, let’s break down their unique roles and how they can be integrated step-by-step.
.webp)
TOC Prioritization + Lean Toolkit: A Strategic Duo:
The Theory of Constraints provides a strategic focus on the one factor that’s holding back performance the bottleneck. In contrast, Lean Manufacturing provides a toolset of methods to optimize the identified bottleneck and improve overall process flow.
Think of TOC as a diagnostic tool that identifies the critical issue and Lean as the prescription that improves and sustains performance.
Here’s how they work together:
Examples of Integration: Lean Tools to Support TOC Steps
Let’s look at specific Lean tools that can be used to address the Five Focusing Steps of TOC and how they enhance the process.
Step 1: Identify the Constraint
The first step in TOC is identifying the bottleneck the point in your system where demand exceeds capacity. This is where Lean tools like Value Stream Mapping and Gemba Walks are incredibly valuable.
- Value Stream Mapping: Helps visualize the entire workflow, making it easier to spot where delays and inefficiencies are occurring.
- Gemba Walks: Involves observing processes on the shop floor to gather real-time insights on potential bottlenecks.
Example: In a manufacturing plant, a company uses Value Stream Mapping to uncover that a particular machine in the assembly line is causing delays. The Gemba Walk confirms that frequent breakdowns are slowing production.
Step 2: Exploit the Constraint
Once the constraint is identified, TOC emphasizes making the most of it without investing additional resources. Lean tools like 5S, Standardized Work, and Visual Factory help optimize the constraint’s performance
- 5S: Organizes the workspace to reduce wasted time and improve efficiency.
- Standardized Work: Ensures that tasks are performed consistently and effectively to reduce variability.
- Visual Factory: Uses visual cues to track the constraint’s performance in real-time.
Example: An IT service team handling customer support tickets identifies a bottleneck in processing escalated cases. They apply Standardized Work to ensure agents follow a consistent approach, reducing handling time and improving throughput.
Step 3: Subordinate Other Processes
In TOC, this step ensures that all other parts of the system are aligned to support the constraint. Lean tools like Kanban and Line Control are perfect for this.
- Kanban: Regulates the flow of work around the constraint by preventing overproduction and limiting work-in-progress.
- Line Control: Synchronizes different parts of the process to ensure that upstream and downstream activities don’t overwhelm the bottleneck.
Example: A hospital experiences delays in its emergency department because diagnostic tests take too long. By implementing Kanban to manage the flow of patient tests and Line Control to synchronize lab work, the hospital reduces wait times and improves patient care.
Step 4: Elevate the Constraint
Once the existing resources are optimized, TOC suggests elevating the constraint by making additional investments to further improve its capacity. Lean tools like TPM (Total Productive Maintenance), SMED (Single-Minute Exchange of Dies), and Poka-Yoke are crucial here.
- TPM: Prevents equipment breakdowns to ensure the constraint remains operational.
- SMED: Reduces changeover times to keep the constraint running longer.
- Poka-Yoke: Ensures that errors don’t occur at the constraint, preventing rework.
Example: A pharmaceutical company struggling with delays in packaging applies TPM to reduce machine downtime and SMED to cut changeover times, increasing throughput without hiring additional staff.
Step 5: Repeat the Process
The final step in TOC is to continuously improve by identifying new constraints as they emerge. Lean practices like Kaizen and Continuous Improvement play a critical role in ensuring that improvements are sustained and ongoing.
- Kaizen: Encourages small, incremental improvements over time.
- Continuous Improvement: Focuses on long-term, sustained process enhancements.
Example: A software development company that improves its code review process by removing bottlenecks continues to apply Kaizen practices to ensure ongoing improvements in coding speed and quality.
Common Misconceptions About TOC and Lean
Misconception #1: TOC and Lean are contradictory.
Truth: TOC focuses on improving one critical point, while Lean provides the tools to improve and sustain that point.
Misconception #2: Lean tools are only for manufacturing.
Truth: Lean tools can be applied in service industries, IT, and healthcare.
Getting Started with TOC + Lean: A Quick Guide
- Start with TOC: Identify your biggest constraint.
- Map the Process: Use Lean tools like Value Stream Mapping and Gemba Walks to visualize the workflow.
- Apply Lean Tools: Use 5S, Kanban, SMED, and TPM to optimize the constraint.
- Monitor and Improve: Use Kaizen and Continuous Improvement to ensure sustained gains.
Real-World Application
Mazda Cut Product Development Time in Half and Return to Profitability
Facing four consecutive years of financial losses, Mazda was on the verge of collapse. The company’s survival depended on developing innovative technology that would rival hybrid engines while maintaining affordable costs and driving pleasure. However, Mazda’s product development cycle was too long, jeopardizing its ability to meet market demands.
In 2007, Mazda began implementing Critical Chain Project Management (CCPM), a Theory of Constraints (TOC) methodology, to streamline their project management processes. By focusing on identifying and managing bottlenecks in their development projects, Mazda was able to cut its product development cycle in half. The successful launch of SKYACTIV technology known for its fuel efficiency and driving performance marked a turning point for the company.
Mazda’s CX-5 SUV, the first vehicle to feature SKYACTIV technology, became a top-selling model and won 73 awards, including Japan Car of the Year. The company returned to profitability in 2013, demonstrating how TOC can drive breakthrough performance in highly competitive industries.
Dr. Reddy’s Laboratories Win the Best Supplier Award in the U.S.
Dr. Reddy’s Laboratories (DRL) faced significant supply chain challenges in the U.S., including high backorders and poor supplier ratings. To address these issues, the company implemented the Theory of Constraints (TOC) to focus on improving inventory management and critical chain project management.
This approach helped streamline manufacturing and R&D pipelines, ensuring DRL focused on fixing the weakest parts of its supply chain. The shift to throughput-based systems simplified accounting, allowing better operational focus.
As a result, DRL significantly reduced backorders, improved supplier ratings, and went on to win the Best Supplier Award in the U.S.
Benefits of the Theory of Constraints
Implementing TOC successfully offers several advantages:
1. Enhancing Capacity: TOC enables companies to increase throughput by optimizing constraints. This allows for faster production rates and higher revenue.
2. Reducing Lead Time: Addressing constraints streamlines workflows, leading to quicker delivery times, improved project processes, and increased customer satisfaction.
3. Adopting a Holistic Approach: TOC focuses on identifying and eliminating constraints and creates a smoother and faster product flow throughout the entire system.
4. Minimizing Waste: TOC reduces excess inventory and work-in-progress by aligning operations with the capacity of constraints , thereby decreasing waste.
Over 5000 organizations from around the world have achieved a major breakthrough with TOC. Let us see some examples of those right away!
- Bajaj Electricals Ltd.: In 2019, Bajaj Electricals aimed for a 20-25% growth. They focused on smart lighting and smart city projects, which contributed to 15-20% of their segment's revenue. By implementing TOC, the company optimized internal processes which lead to improved project delivery and operational efficiency.
- Dr. Reddy’s Laboratories: Facing high backorders and low supplier ratings in the U.S., Dr. Reddy’s adopted TOC. This strategic move enhanced their supply chain management and improved supplier ratings and operational performance.
- Morphy Richards: The consumer durables brand implemented TOC to address stock outs and excess inventory at distributor levels. This initiative resulted in a 40% optimization of working capital and streamlined sales processes.
- Lithuania: The country embarked on a nationwide TOC implementation to boost its GDP. By applying TOC to various sectors, including healthcare and education, Lithuania achieved significant improvements in lead times and operational efficiency.
- Mazda: Facing financial challenges, Mazda adopted TOC to enhance product development cycles. This approach halved development durations and improved project delivery and contributed to the company's turnaround.
Frequently Asked Questions
Conclusion
The Theory of Constraints offers strong points for established organizations by targeting operational bottlenecks, though its rapid-response approach may not suit every context, particularly for startups needing to balance quick wins with strategic planning. While its focus on immediate obstacles can drive impressive short-term gains, organizations must thoughtfully evaluate whether this methodology aligns with their broader objectives and maturity level. Fortunately, companies don't have to scour through these challenges alone.
Through comprehensive solutions like Edstellar's instructor-led corporate training, organizations can access a global network of over 5,000+ certified trainers who enable employees to identify and address operational constraints. By combining strategic learning interventions with sophisticated training management, companies can transform their constraints into catalysts for breakthrough performance, all while maintaining the flexibility to test and adapt the approach to their specific needs.
This approach allows organizations to continuously improve, helping teams tackle current challenges while staying flexible enough to adapt to future changes, ultimately leading to improved efficiency, higher productivity, and better business outcomes.
Explore High-impact instructor-led training for your teams.
#On-site #Virtual #GroupTraining #Customized
Edstellar Training Catalog
Explore 2000+ industry ready instructor-led training programs.
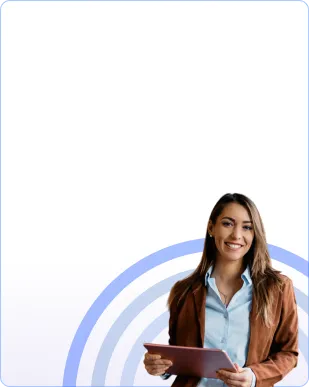
Coaching that Unlocks Potential
Create dynamic leaders and cohesive teams. Learn more now!
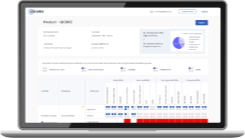
Want to evaluate your team’s skill gaps?
Do a quick Skill gap analysis with Edstellar’s Free Skill Matrix tool
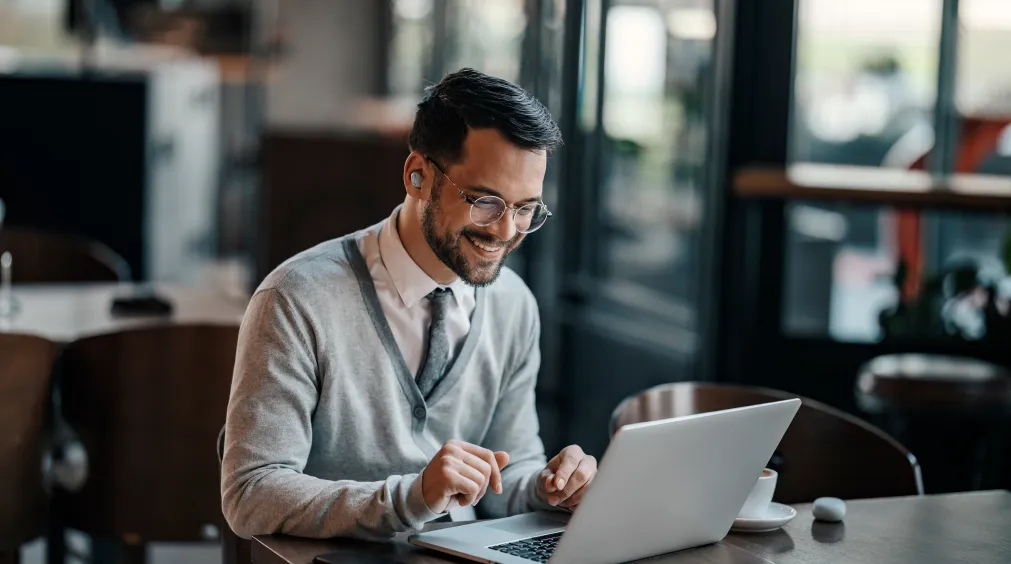
Transform Your L&D Strategy Today
Unlock premium resources, tools, and frameworks designed for HR and learning professionals. Our L&D Hub gives you everything needed to elevate your organization's training approach.
Access L&D Hub Resources