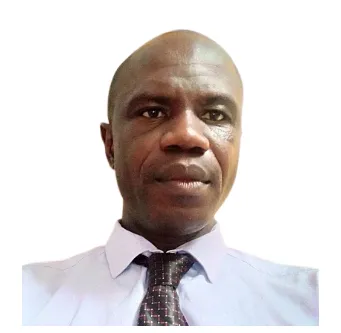
Samuel
PRINCE2 Foundation Trainer in Lagos
Samuel is a seasoned professional with an impressive track record of over 15 years in the Steel Industry, FMCG (Flour Mills Nig. PLC), SAB Miller, ABInBev, Chemical and Allied Products Plc (CAP PLC), and Nigerian Bottling Company (Coca-Cola HBC Nigeria). His diverse experience spans various sectors, including Food and Beverages Industries. Samuel boasts many skills and expertise, making him a valuable asset in any organization. His strengths encompass Production & Process, Maintenance, Marketing, WCM, Lean Manufacturing, Total Productive Maintenance (JIPM Methodology), 5S, Manufacturing Way/Excellence, Voyager Plant Optimization (VPO), Training and Consultancy, Maintenance Planning/Scheduling, Zero Based Budgeting, Project Planning, and Project Management.
His unwavering passion for continuous improvement and knowledge sharing sets Samuel apart. He is dedicated to enhancing processes and operations and committed to imparting his wealth of knowledge to others. With a career marked by a series of successes across different industries, Samuel is a testament to the power of expertise, dedication, and a commitment to excellence. His impressive journey in the corporate world is a testament to his unwavering dedication to continuous growth and the betterment of the organizations he serves.