The manufacturing industry is undergoing a pivotal change with digital manufacturing transformation, redefining factory operations, product creation, and the delivery of value to customers. Industry projections suggest that by 2027, global spending on digital transformation will reach nearly $3.7 trillion, with the manufacturing sector at the forefront. This transformation is driven by powerful technologies like artificial intelligence (AI), robotics, the Internet of Things (IoT), automation, and big data analytics, all of which are helping manufacturers unlock new levels of efficiency, quality, and innovation.
This transformation is not merely about adopting new tools or machines; it’s about fundamentally reshaping the entire manufacturing landscape to meet the needs of a dynamic market. With the rise of Industry 4.0, manufacturers are striving to remain competitive in an environment that demands speed, agility, and cost-effectiveness. Manufacturing digital transformation enables manufacturers to achieve these goals by integrating their entire operation from supply chains and production lines to maintenance and workforce management using smart technologies.
The urgency of digital transformation is evident in the numbers. McKinsey notes that today’s digitally-enabled factories have evolved significantly from the top factories of a decade ago. With advancements in data analytics, AI, and machine learning and a growing variety of technology providers manufacturers now have access to hundreds of solutions to enhance their operations. When implemented effectively, these technologies offer compelling returns. Across industries, as per McKinsey, results often include 30–50% reductions in machine downtime, 10–30% boosts in throughput, 15–30% gains in labor productivity, and an 85% increase in forecasting accuracy.
Besides, the 2022 PwC Digital Factory Transformation Survey reveals that only 10% of companies are fully digitized, with many still in the early stages, hindered by complex systems and machine diversity. Digital champions, however, show that comprehensive digital adoption can drive both resilience and cost efficiency.
Further, as per Deloitte’s survey on the future of the digital customer experience in industrial manufacturing and construction; over 80% of respondents said their company is either currently using or planning to invest in digital technologies like CRM systems, cloud computing, IoT, robotics, and automation. Many also indicated an increased focus on emerging technologies, including AI, machine learning, generative AI, and extended reality, reflecting the sector's commitment to digital innovation. Additionally, 93% are testing or applying at least one digital customer experience (DCX) initiative, with an average of four in progress.
Moreover, the global smart manufacturing market, valued at USD 292.83 billion in 2023, is projected to grow at a compound annual growth rate (CAGR) of 15.18% from 2024 to 2033, reaching an estimated USD 1,203.38 billion by 2033.
Ultimately, to succeed in this digital era, manufacturers must adopt cutting-edge tools and develop the skills necessary to lead their organizations through this complex transition. Key skills, such as data analytics, AI and machine learning, cloud computing, and cybersecurity, are now essential for manufacturing teams to remain competitive and innovative. Studies show that over 90% of manufacturing leaders view digital transformation as critical to their success, highlighting the high stakes. Besides, AI is central to digital transformation, driving automation, uncovering data-driven insights, and supporting strategic decision-making.
This guide explores every facet of the digital transformation of manufacturing, offering detailed insights into the importance of this shift, the technologies involved, and the benefits it offers. It also breaks down each step and shows how manufacturers can strategically leverage these technologies to improve efficiency, streamline operations, and create new business models. Let’s dive in.
What is Digital Transformation in Manufacturing?
The digital transformation of manufacturing involves integrating digital technologies into every aspect of the manufacturing process. This transformation extends from product design to production, supply chain management, and customer service, enabling manufacturers to optimize operations and make better-informed decisions through data. It essentially involves applying smart technologies, like the IoT, AI, and advanced analytics, which lead to greater automation, real-time insights, and more adaptable production workflows.
In practice, digital transformation is driven by tools that collect and analyze data to improve efficiency and quality. For instance, IoT devices gather data from machinery, sensors, and products on the factory floor. AI then processes this data, helping to predict equipment failures, optimize production schedules, and enhance quality control. With real-time data streaming from various parts of the manufacturing line, decision-making becomes faster and more accurate, allowing for dynamic adjustments and proactive solutions to potential issues.
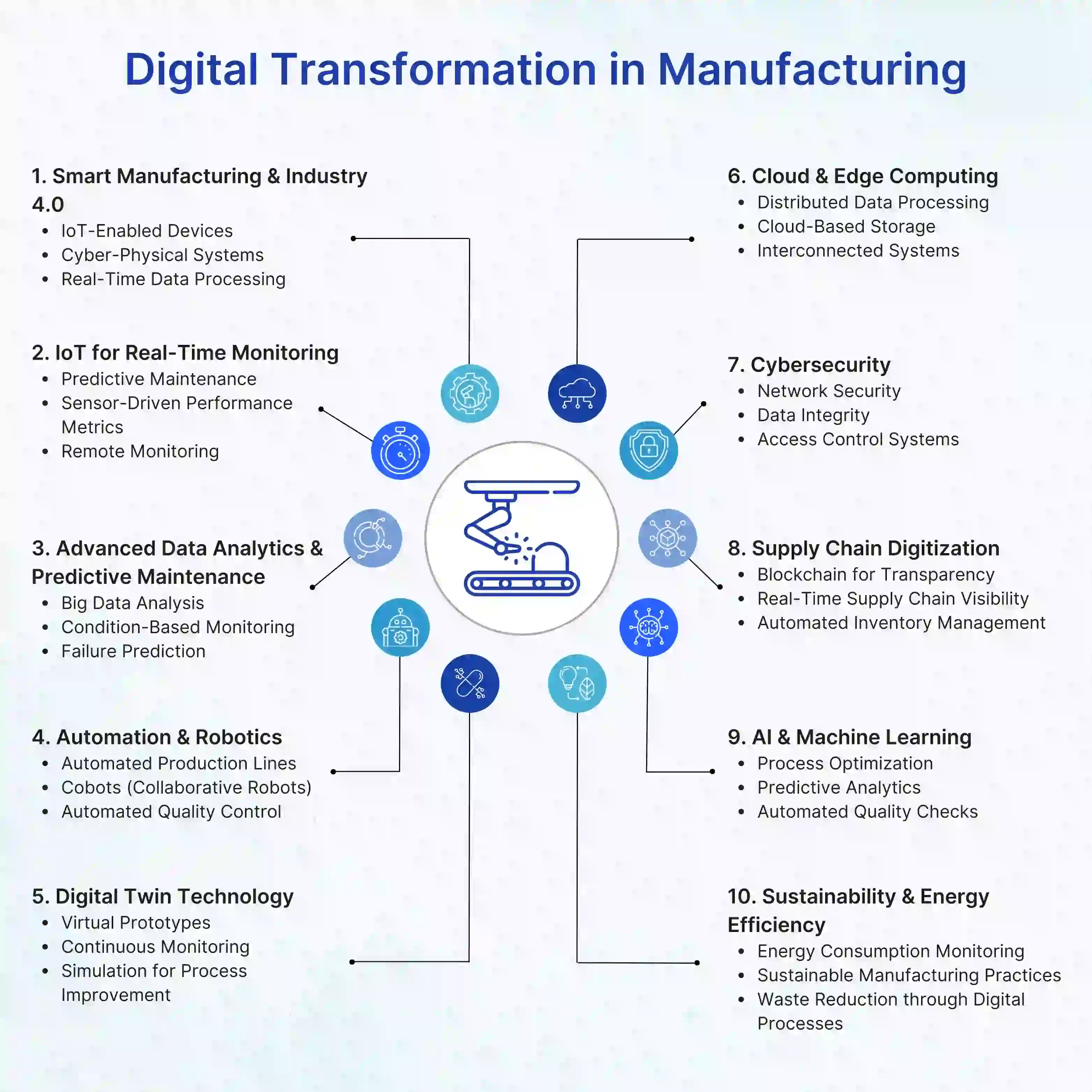
Why is Digital Transformation Important in Manufacturing?
Below are key reasons why digital transformation is essential in modern manufacturing:
1. Enhanced Productivity and Efficiency:
Digital transformation introduces advanced technologies that streamline workflows and automate tasks that were previously manual, reducing time and effort. Integrating IoT and AI systems allows manufacturers to monitor production lines in real time, identifying any inefficiencies or bottlenecks immediately.
This approach ensures that resources are allocated optimally, and that downtime is minimized through predictive maintenance and effective resource management. Automation also allows workers to focus on more strategic and skilled tasks, improving overall workforce efficiency. The result is a more productive manufacturing environment where all processes are aligned to drive faster output and better results.
2. Cost Reduction:
Implementing digital transformation can substantially lower operational costs across the board by improving asset utilization and reducing wastage. With technologies like predictive maintenance, manufacturers can prevent costly equipment breakdowns and avoid the expense associated with unplanned downtime.
Real-time monitoring of materials and energy consumption also leads to smarter resource management, decreasing waste and lowering associated costs. Additionally, automated quality control can reduce the financial burden of product recalls and rework by ensuring defects are caught early. Overall, digital initiatives allow for better cost management, allowing companies to allocate their budgets more effectively and increase profitability.
3. Improved Quality Control:
Advanced digital tools bring a new level of precision to quality control, enabling real-time monitoring and immediate response to quality issues. AI-driven quality checks can identify defects or inconsistencies across products, maintaining high standards and reducing the likelihood of faulty products reaching customers. This leads to more consistent product quality, which enhances customer satisfaction and brand loyalty.
Detailed data analytics further refine quality control processes, offering insights into areas for improvement and helping manufacturers proactively address potential issues. Over time, such technologies create a reputation for reliability, which is invaluable in today’s competitive market.
4. Supply Chain Optimization:
Digital transformation enhances visibility across the supply chain, providing insights into supplier performance, inventory levels, and potential disruptions. With a clearer view of supply and demand dynamics, manufacturers can optimize inventory management, ensuring they have the right amount of stock at the right time. This approach minimizes stockouts and overstock scenarios, reducing waste and storage costs.
Technologies such as blockchain and IoT allow for real-time tracking of goods, which improves transparency and accountability throughout the supply chain. The outcome is a more resilient supply chain, equipped to handle market fluctuations and unexpected challenges more effectively.
5. Agility in Responding to Market Changes:
Modern manufacturing requires a level of agility that traditional methods need help to provide. Digital transformation empowers manufacturers to adjust quickly to shifts in market demands, whether through flexible production lines or rapid data-driven adjustments. Manufacturers can experiment with new products, production techniques, or customizations that better meet customer expectations, fostering innovation.
Additionally, agile digital systems make it possible to scale production up or down depending on demand, reducing costs during low-demand periods. This level of adaptability ensures that manufacturers remain competitive and relevant, regardless of market conditions.
6. Enhanced Collaboration and Communication:
Digital platforms improve collaboration across different departments by providing a centralized space for information sharing and project tracking. With all team members accessing the same data and insights, there is better alignment on goals, which supports faster and more effective decision-making. Enhanced communication between departments reduces the risk of misalignment, ensuring all teams work toward shared objectives efficiently.
Cloud-based platforms enable instant communication, which supports real-time problem-solving and innovation. The unified approach strengthens teamwork and drives better results by promoting a culture of transparency and accountability.
7. Data-Driven Decision-Making:
Access to accurate, real-time data transforms the way manufacturers make decisions, allowing for a strategic approach based on actual performance metrics rather than guesswork. Data analytics reveals trends and patterns within production and supply chain processes, helping leaders identify areas that need improvement or adjustment.
Analyzing data trends also supports proactive planning, as manufacturers can anticipate market shifts or operational challenges and prepare accordingly. Data-based decisions also build confidence among stakeholders, as the evidence is clear and reliable. The strategic value of data-driven insights contributes to more efficient and effective operations, enhancing profitability and competitive advantage.
8. Sustainability and Waste Reduction:
Digital transformation enables manufacturers to measure and manage their environmental impact more effectively, aligning with sustainability goals and regulatory requirements. Real-time monitoring tools track resource usage, allowing manufacturers to identify areas where energy or materials may be overused. This careful resource management reduces waste and promotes recycling, lowering the overall environmental footprint.
Sustainability initiatives also strengthen a company’s brand image, as customers and investors increasingly value environmentally responsible practices. Embedding sustainable practices into everyday operations contributes to a long-term positive impact on the environment and sets the stage for a more eco-friendly industry.
Technologies Helping Digital Transformation in Manufacturing
- Predictive Maintenance with AI and IoT:
Predictive maintenance uses AI and IoT to monitor equipment in real time, detecting early signs of wear and ensuring timely maintenance. This approach reduces maintenance costs, extends equipment lifespan, and minimizes downtime. AI algorithms analyze sensor data to predict when machinery will need maintenance, allowing issues to be addressed before they disrupt production.
IoT sensors track equipment condition, monitor production lines, and assess quality, optimizing the entire manufacturing process. By preventing unexpected failures, predictive maintenance enhances operational efficiency and safety, contributing to a smoother, more reliable production environment.
- AI in Quality Control:
AI-driven quality control is transforming how manufacturers ensure product consistency and detect defects. Advanced machine learning algorithms analyze production line data in real-time, identifying defects or quality issues far quicker than human inspectors. These systems detect even minute irregularities in size, texture, or color, enabling immediate correction, often before a batch is completed.
As AI systems continuously learn and improve, their accuracy and efficiency grow over time. By automating quality control, manufacturers reduce human error, enhance product quality, and maintain high standards without disrupting production.
- Robotic Process Automation (RPA) for Operational Efficiency:
RPA automates repetitive tasks traditionally handled by humans, such as data entry, order processing, inventory management, and compliance reporting. In manufacturing, RPA streamlines operations, working faster and more accurately than human workers. It operates around the clock, freeing up human resources for higher-level tasks that require critical thinking.
RPA integrates easily with legacy systems, making it a cost-effective solution for modernizing operations. Improving productivity, reducing costs, and minimizing errors, RPA ensures routine tasks are completed efficiently.
- Additive Manufacturing (AM):
AM, or 3D printing, is transforming the manufacturing sector by enabling on-demand production of complex parts without traditional molds or tooling. This technology allows for the creation of customized products with minimal material usage, reducing waste and enhancing sustainability. AM is especially effective for small batches and prototypes, where conventional methods can be costly or time-consuming.
It accelerates time to market, offers design flexibility, and fosters innovation. With easier design iteration, manufacturers can quickly adapt to market changes. Furthermore, integrating 3D printing into supply chains reduces reliance on costly inventory and helps avoid obsolescence.
- Cobots for Increased Flexibility and Productivity:
Collaborative robots, or cobots, are designed to work alongside human operators in a shared workspace. Unlike traditional robots, which often operate in isolated environments, cobots can perform repetitive or physically demanding tasks while interacting with human workers. This integration of human labor and robotics increases manufacturing productivity and safety.
Cobots can be easily programmed and reprogrammed to perform a variety of tasks, offering manufacturers flexibility to adapt to different production needs. They also help improve worker ergonomics by handling tasks that could cause strain or injury, allowing employees to focus on more complex and creative aspects of the job.
- Cloud Computing for Scalable Operations:
Cloud computing in manufacturing provides flexibility and scalability by offering on-demand access to computing resources. Manufacturers can securely store large volumes of data in the cloud, making it accessible across various locations. This enhances collaboration, simplifies system integration, and allows for the quick deployment of new digital tools without the need for extensive on-site infrastructure.
Cloud computing streamlines operations and enables manufacturers to scale production according to market demand. It also drives innovation by providing access to advanced technologies like AI, IoT, and big data analytics, helping manufacturers stay competitive.
- Blockchain for Traceability and Compliance:
Blockchain technology provides manufacturers with a secure and transparent method for tracking materials and products throughout the supply chain. Using a decentralized ledger, blockchain ensures that all transactions are tamper-proof and verifiable, which is essential for regulatory compliance and quality assurance. It creates immutable records of materials, components, and product histories, helping ensure products meet safety and environmental standards.
Blockchain also improves traceability, enabling manufacturers to quickly address supply chain disruptions or product recalls. Its transparency builds trust with consumers and partners by demonstrating ethical sourcing and regulatory adherence, simplifying compliance with international standards in global supply chains.
- Generative Design for Optimized Production Efficiency:
Generative design uses AI to generate a variety of optimized product designs based on parameters such as material type, weight limits, and production methods. This technology enables manufacturers to create the most efficient designs, reducing material waste while maintaining product durability and functionality.
Generative design allows manufacturers to explore numerous design alternatives, often revealing solutions that traditional methods might overlook. It not only leads to cost savings by minimizing excess material but also supports sustainability by lowering environmental impact. Additionally, it improves product performance by optimizing geometry for strength, lightness, and resistance, resulting in more advanced and efficient products.
- Augmented Reality (AR) for Training and Maintenance:
With AR, technicians can overlay digital information on physical objects, guiding them through complex maintenance tasks or assembly processes. This reduces errors, increases efficiency, and speeds up training for new employees. AR also provides real-time support by offering remote assistance from experts who can see what the technician sees through AR glasses or a mobile device.
In manufacturing, AR helps technicians repair machinery more effectively and trains workers in simulated environments before they handle real-world tasks, minimizing risks and improving skill development.
- Digital Twin Ecosystems Beyond Product Simulation:
Digital twin technology creates virtual replicas of physical assets, products, or systems, allowing manufacturers to simulate and optimize operations. These digital models enable real-time monitoring of equipment and production processes, helping predict and prevent failures, optimize energy use, and test configurations without affecting actual production.
Leveraging AI-driven insights and real-time data, digital twins reduce waste, improve profits, and minimize emissions. They enhance collaboration across industrial ecosystems, providing sustainable solutions and increased efficiency, though requiring new governance and data-sharing systems. Digital twins offer advanced visibility into supply chain performance, from raw material procurement to product delivery, helping manufacturers adjust processes to meet sustainability goals and reduce waste.
Manufacturing Transformation in Action: How Core Manufacturing Processes Have Evolved
Here are manufacturing transformation insights highlighting how core manufacturing processes have evolved through digital transformation, along with the key technologies driving these changes and the significant benefits they offer to manufacturers.
The 9-Phase Process of Digital Transformation in Manufacturing
The shift toward digital technologies empowers manufacturers to remain competitive, adapt to market demands, and meet sustainability goals for long-term success. The following are the 9 key phases involved in digital transformation for manufacturing:
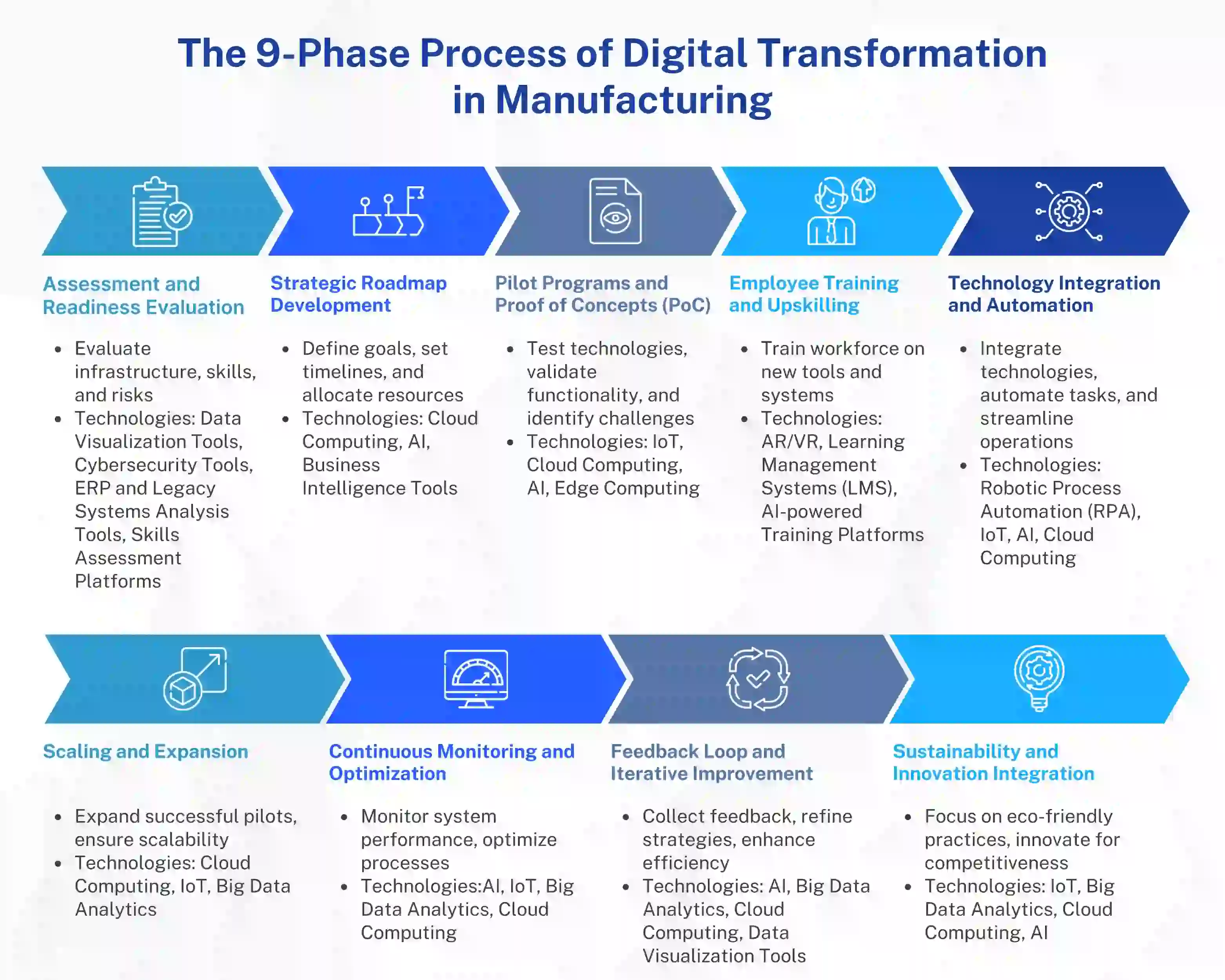
1. Assessment and Readiness Evaluation
This phase involves evaluating the current state of manufacturing operations to determine the organization's readiness for digital transformation. Manufacturers assess existing infrastructure, technology stacks, workforce skills, and organizational culture to identify potential barriers to change. A comprehensive evaluation highlights gaps in technology, efficiency, and processes that need to be addressed. It ensures management and teams are aligned on the goals and objectives of the transformation. The outcome of this phase sets the foundation for the rest of the digital transformation process, ensuring a clear understanding of what needs to be achieved.
2. Strategic Roadmap Development
Once readiness is assessed, the next step is creating a strategic roadmap outlining the digital transformation journey. This roadmap includes clear goals, timelines, and milestones to guide the organization’s digital initiatives. It addresses which technologies will be implemented, how they will be integrated, and how they align with long-term business goals. The roadmap also identifies the necessary resources, budgets, and skill requirements for each phase of the transformation. The strategic roadmap provides a structured plan to follow and ensures alignment across all departments and stakeholders.
3. Pilot Programs and Proof of Concepts (PoC)
Before fully scaling new technologies, manufacturers conduct pilot programs or proof of concepts (PoCs) to test their feasibility and effectiveness. This allows businesses to validate the technology in a controlled environment and assess how well it meets specific operational needs. PoCs help identify potential challenges and fine-tune solutions before committing to full-scale deployment. These smaller-scale experiments demonstrate tangible results and benefits, building confidence among employees and leadership.
4. Employee Training and Upskilling
Employee training and upskilling ensure that the workforce can effectively operate and leverage new digital technologies. In this phase, manufacturers invest in training programs that provide employees with the necessary skills to use new software, machinery, or automation systems. Upskilling not only helps workers adapt to new technologies but also fosters innovation and improves job satisfaction.
Employees learn how digital tools integrate with existing processes and enhance productivity. Continuous skill development ensures the workforce remains agile, capable of maintaining competitive advantages in a rapidly evolving manufacturing landscape.
5. Technology Integration and Automation
After selecting the right technologies, the next phase is integrating them into existing systems and processes. This could involve implementing AI-driven systems, automation tools, or advanced data analytics into manufacturing operations. The focus is on streamlining workflows, improving operational efficiency, and reducing manual errors. Integrating technologies also enables seamless communication between different departments, improving coordination and decision-making.
Automation eliminates repetitive tasks, freeing up workers to focus on more strategic roles. Successful integration requires strong collaboration between IT and operations teams to ensure smooth deployment and minimal disruption.
6. Scaling and Expansion
Once pilot programs have proven successful, the next step is scaling the digital transformation efforts across the entire manufacturing process. This includes expanding automation and digital tools to other areas, such as supply chain management, inventory tracking, and production scheduling. Scaling also involves ensuring that the infrastructure can handle increased data flow and processing demands. Manufacturers must ensure new digital systems are compatible with existing legacy systems. Expanding digital transformation drives efficiencies across the organization, creating a more connected and responsive operation that adapts to market changes.
7. Continuous Monitoring and Optimization
Continuous monitoring and optimization are essential to maintaining the effectiveness of digital solutions in manufacturing. Using real-time data, manufacturers track the performance of production lines, equipment, and supply chains to ensure everything operates at peak efficiency. Key performance indicators (KPIs) are monitored to identify areas needing improvement. This phase also adjusts parameters based on real-time feedback to optimize energy usage, reduce waste, and prevent downtime. Continuous optimization helps manufacturers stay competitive by ensuring operations always improve and adapt to changing market demands.
8. Feedback Loop and Iterative Improvement
This phase involves gathering feedback from employees, customers, and digital systems to identify areas for improvement. Continuous feedback loops allow manufacturers to refine and enhance digital tools, processes, and strategies over time. Iterative improvement ensures digital transformation is an ongoing journey, not a one-time effort. Analyzing performance data and employee insights leads to adjustments that optimize the impact of digital technologies. This process ensures the organization remains flexible and responsive, contributing to incremental improvements that increase long-term efficiency and innovation.
9. Sustainability and Innovation Integration
The final phase focuses on ensuring sustainability and innovation are core components of digital transformation. Manufacturers integrate sustainable practices into their processes, such as reducing waste, lowering carbon emissions, and utilizing eco-friendly materials. Innovation plays a significant role in creating products that meet evolving customer needs while maintaining environmental responsibility.
Digital technologies like AI, IoT, and blockchain help optimize resource use and ensure compliance with environmental standards. As manufacturers continue their digital transformation, they focus on staying ahead of industry trends and continuously pushing for innovation to maintain competitiveness and meet sustainability goals.
By following these phases, manufacturers can ensure that their digital transformation journey is strategic, efficient, and aligned with long-term business goals.
Is Your Team Equipped with the Skills to Lead Digital Transformation in Manufacturing?
To lead a successful digital transformation, manufacturing leaders and management teams need a blend of technical, strategic, and analytical skills to manage and guide their teams through evolving industry demands. Digital transformation in manufacturing goes far beyond adopting IoT, AI, and automation; it requires digital transformation leadership skills that help strategize priorities, drive operational efficiency, and cultivate a resilient, innovative workforce. Below is a roadmap of essential tips and necessary skills for leaders in the manufacturing sector.
1. Strategic Vision and Digital Literacy for Manufacturing
Strategic vision and digital literacy are foundational skills for manufacturing leaders. A strong strategic vision ensures that digital technologies are aligned with the overall business objectives, enabling growth, operational efficiency, and market competitiveness. Digital literacy, particularly in technologies like AI, IoT, and robotics, is essential for understanding how these innovations can be applied to enhance production processes, quality control, and decision-making.
Leaders with this skill can identify opportunities for automation, data-driven improvements, and cost savings. They are better equipped to navigate the complexities of digital transformation and lead teams effectively through changes. This competency ultimately drives long-term success by ensuring that digital tools are not only adopted but also utilized to their full potential, improving both the top and bottom lines.
2. Staying Current with Essential Manufacturing Competencies
As manufacturing evolves with the advent of automation and digital tools, reskilling and upskilling become crucial for workforce adaptability. Leaders need to ensure that their teams are well-equipped to manage new technologies like robotics, AI-based quality control systems, and data analytics tools. For example, a workforce trained in automation can handle robotic machines efficiently, increasing production speed and precision. Knowledge in data analytics allows teams to harness data from IoT devices and predictive maintenance tools to enhance operations and reduce downtime.
Reskilling initiatives also prepare employees for the complexities of advanced machinery, ensuring smooth production cycles and minimal equipment malfunctions. Investing in continuous training programs is essential for fostering a knowledgeable workforce that can adapt to new tools and methodologies, contributing directly to the organization’s operational success.
3. Management of Manufacturing Change and Adaptability
In the context of digital transformation, change management and adaptability are key to minimizing resistance and ensuring smooth transitions. Manufacturing leaders with strong change management skills can guide teams through technological shifts, such as the integration of AI or IoT into production systems. Effective communication and conflict resolution skills help to address concerns and maintain morale during transitions.
By fostering an organizational culture that embraces change, leaders can reduce friction, allowing employees to focus on maximizing the potential of new tools. Adaptability is especially critical in industries where market demands change rapidly and the technology landscape continuously evolves. Leaders who prioritize change management help ensure that the workforce remains engaged and agile, continuously improving in line with technological advancements.
4. Develop Technical Proficiency in Emerging Manufacturing Technologies
Having technical proficiency in emerging technologies like digital twins, cobots, and additive manufacturing is crucial for leaders in the manufacturing sector. While they may not need an engineering background, understanding how these technologies work helps leaders make informed decisions regarding investments and implementation. For example, a leader well-versed in digital twins can make better choices about virtual simulations, optimizing processes, and predicting potential equipment failures.
Similarly, knowledge of cobots enables leaders to integrate collaborative robots into production lines, enhancing flexibility and efficiency without replacing human workers. Leaders with a solid understanding of these technologies can work closely with technical teams, ensuring that new tools are implemented effectively and provide the anticipated operational benefits, from improving productivity to reducing costs.
5. Managing Cybersecurity Risks in Manufacturing
As manufacturing becomes increasingly connected, cybersecurity and risk management skills are essential to protect intellectual property, operational data, and digital systems. Leaders need to understand how to secure data from IoT devices, cloud platforms, and industrial control systems from cyber threats. Cybersecurity training empowers leaders to recognize vulnerabilities and take proactive measures, such as implementing encryption, access controls, and regular audits.
These skills are especially important in the context of Industry 4.0, where operational technology and IT systems are closely integrated, increasing the risk of cyberattacks. Effective risk management strategies also help to mitigate operational disruptions caused by data breaches or system failures. Manufacturing leaders with a strong grasp of cybersecurity and risk management not only protect their organization’s assets but also ensure business continuity and compliance with regulatory standards.
6. Knowledge of Supply Chain and Blockchain in Manufacturing
The digital transformation in the manufacturing market has expanded into supply chain management, making it essential for leaders to grasp how digital tools like blockchain can improve traceability and transparency. Blockchain technology, for example, enables manufacturers to track materials and products through every step of the supply chain, ensuring accountability and compliance with regulatory standards. Knowledge of digital supply chain management also helps leaders optimize inventory management, reduce waste, and improve supplier relationships.
With real-time visibility into supply chain operations, manufacturers can reduce lead times, manage risks more effectively, and respond quickly to disruptions. Leaders skilled in supply chain management can also streamline procurement processes, improving the efficiency of global supply chains and ensuring product availability. Ultimately, these skills help manufacturers increase their operational efficiency, improve customer satisfaction, and maintain regulatory compliance.
7. Using IoT to Forecast Demand for Manufacturing with a Customer-centric Mindset
A customer-centric mindset, supported by IoT-driven demand forecasting, is essential for manufacturing leaders looking to remain competitive. IoT devices provide real-time data that enables manufacturers to track customer preferences, monitor demand trends, and align production schedules with market needs. Leaders who leverage this data can optimize inventory management and production processes, reducing waste and improving profitability. A customer-centric approach also fosters stronger relationships with clients by enabling manufacturers to deliver customized products and services that meet exact requirements.
Having your team advance their IoT skills drives success. Additionally, by understanding customer demand through IoT insights, leaders can better anticipate market shifts, making their operations more responsive and agile. This skill ensures that manufacturing decisions are driven by customer needs, providing a competitive edge in an increasingly consumer-driven market.
8. Sustainability Awareness and Environmental Knowledge in Manufacturing
With growing pressure from regulators and consumers, sustainability is a critical focus for manufacturers. Leaders who are aware of how digital tools can support eco-friendly practices have a significant advantage in today’s manufacturing landscape. Technologies like AI, IoT, and analytics can help optimize energy usage, reduce material waste, and improve sustainability in production processes. Leaders skilled in sustainability can identify opportunities to enhance environmental compliance while maintaining or increasing production efficiency.
They can also align digital transformation initiatives with sustainability goals, ensuring the long-term viability of their operations. Moreover, sustainability awareness boosts a manufacturer’s brand reputation, appealing to environmentally-conscious consumers and fostering goodwill with regulatory bodies. As a result, manufacturing leaders must prioritize eco-friendly practices as a core part of their digital transformation strategy.
9. Digital Manufacturing Project Management
Effective project management is vital for overseeing digital transformation initiatives in manufacturing. Leaders must manage multiple projects, such as the implementation of new technologies or the rollout of digital tools across production lines. Strong project management skills ensure that resources are allocated efficiently, timelines are adhered to, and budgets are maintained. Training in project management methodologies like Agile and Lean can equip leaders with techniques that are well-suited to the fast-paced demands of digital transformation leadership in manufacturing.
This ability to manage projects effectively ensures that digital initiatives are deployed successfully, yielding tangible results like improved efficiency, cost savings, and enhanced product quality. Project management skills are particularly important in complex, cross-functional digital transformation efforts, where coordination and communication between teams are critical to success.
10. Talent Development and Digital Training in Manufacturing
A crucial factor in the digital transformation in the manufacturing market is the continuous development of a workforce with the essential digital skills. Leaders must champion digital training and foster a culture of continuous learning to ensure that teams remain adaptable and capable of handling new technologies. Initiating mentorship programs and creating collaborative learning environments enables teams to stay updated on the latest digital trends and tools.
This approach not only supports individual growth but also ensures that the organization can respond quickly to industry changes. Leadership in talent development also involves guiding teams through the complexities of digital transformation, helping them build the necessary skills to leverage new tools effectively. Manufacturers with strong leadership in this area are well-positioned to drive innovation and maintain a competitive edge in an ever-evolving digital landscape.
Another important skill is familiarity with industry-specific software. Many factories rely on specialized software for planning, scheduling, and tracking operations. Training workers in programs like Manufacturing Execution Systems (MES), Enterprise Resource Planning (ERP), and Computer-Aided Design (CAD) software ensures they can work effectively within these frameworks, improving productivity and accuracy. Besides, proficiency with tools like digital twins, AR, and simulation software helps employees troubleshoot issues in real-time. For instance, AR can be used to visualize complex instructions, making it easier for workers to carry out precise tasks without error.
Building a Digitally Skilled Workforce with Educational Partnerships, Online Training, and Corporate Leadership Development
To support digital transformation in manufacturing, companies are leveraging educational partnerships, online learning platforms, and corporate leadership development to equip their workforce with essential digital and leadership skills. Strategic partnerships with universities and technical schools enable customized training programs focusing on automation, data analytics, IoT, and robotics, preparing graduates for roles in advanced manufacturing. Through internships and apprenticeships, students gain practical, hands-on experience, allowing them to transition seamlessly into tech-driven roles within the manufacturing sector.
Continuous learning pathways for current employees ensure skills are regularly updated to match the industry’s rapid technological advancements. In addition, online training platforms offer on-demand courses in essential areas like cybersecurity for manufacturing systems, digital supply chain management, predictive maintenance, AI-driven data analysis, and project management for digital initiatives. These online resources enable manufacturing teams to acquire the specialized skills needed for Industry 4.0 without disrupting day-to-day operations.
Corporate digital transformation leadership training develops leaders who can drive strategic change. Programs that cultivate corporate leadership focus on skills such as change management, strategic vision for aligning digital tools with business objectives, and effective communication for fostering a culture of innovation and continuous improvement. By nurturing leadership skills, companies ensure that their teams are prepared to manage and motivate employees through complex digital shifts. Besides, corporate manufacturing operations training course helps to develop skills for effective management and operation within the manufacturing sector.
Educational partnerships, online resources, and leadership training create a well-rounded approach that builds a digitally proficient, adaptable, and forward-thinking workforce. This strategy supports sustainable digital transformation and positions manufacturing companies for long-term growth and competitive advantage in a rapidly evolving industry.
Top Challenges Manufacturing Companies Face During Digital Transformation
Digital transformation presents manufacturing companies with unique challenges. While digital technologies promise enhanced efficiency and innovation, the journey often encounters obstacles that can delay or derail transformation efforts. Here are some of the major challenges that manufacturing companies face:
- Legacy Systems and Infrastructure: Many manufacturing companies operate on outdated systems and machinery that weren’t built with modern digital integration in mind. Legacy equipment can be difficult to connect to digital networks, leading to data silos and fragmented processes. Updating these systems can be costly and disruptive, requiring a phased approach to gradually modernize infrastructure without halting production.
- Maintaining Operational Continuity: Introducing new technologies or upgrading existing infrastructure without disrupting daily operations is a constant challenge. Manufacturing companies risk productivity losses or increased downtime during digital upgrades. Strategic planning, phased rollouts, and contingency measures can help companies navigate this transition smoothly, maintaining operational continuity while integrating new tools.
- Supplier and Partner Collaboration: Digital transformation typically requires collaboration with suppliers, distributors, and other external partners. Misalignment in technological capabilities or digital maturity between manufacturers and their partners can lead to integration issues and reduced efficiency. To address this, companies should engage partners early in the process, ensuring they are on board with digital initiatives and aligned on data-sharing and technology standards.
- IT/OT Convergence: In traditional manufacturing, IT (Information Technology) and OT (Operational Technology) functioned as separate entities, often leading to a disconnect between enterprise-level operations and the shop floor. IT, responsible for processing and analyzing data, supports decision-making, while OT manages factory equipment, ensuring efficient production.
As digital transformation advances, converging IT and OT is essential for smarter manufacturing. Integrated systems enhance data flow, optimizing equipment efficiency and providing insights that improve operational decisions. However, IT/OT integration introduces cybersecurity risks, as OT systems historically lack the robust defenses of IT. Manufacturing leaders must adopt a comprehensive strategy, investing in corporate cybersecurity and bridging skill gaps through reskilling to successfully merge IT and OT for digital-first operations.
- Cybersecurity Risks: As manufacturing operations become increasingly connected, cybersecurity risks rise. The adoption of IoT devices, sensors, and cloud solutions increases the potential for cyber threats. Manufacturing companies frequently lack specialized cybersecurity resources, making them more vulnerable to attacks that could disrupt production or lead to data theft. Effective cybersecurity measures, including corporate cybersecurity risk management training and robust data protection protocols, are essential but challenging to implement.
- Resistance to Change: A significant hurdle in digital transformation is overcoming resistance to change, especially within long-standing teams used to traditional processes. Employees may feel uncertain about new technology replacing or complicating their roles, leading to low adoption rates. To counter this, companies need to focus on change management with the right skills and invest in comprehensive training programs that emphasize the benefits of transformation for all team members.
- Skill Gaps and Workforce Training: Digital transformation demands new skills, from data analysis to machine learning, which may not be readily available in the existing workforce. Addressing this skills gap requires extensive training and upskilling, especially for technical and leadership roles. Developing a roadmap for skills development, including certifications and ongoing training, is essential to equip teams with the expertise needed for digital success.
- Data Management and Integration: Manufacturing generates massive volumes of data across various departments, from supply chains to production lines. Managing and integrating this data for effective analysis is complex. Many companies struggle to implement a unified data management system that can break down silos and ensure accurate, real-time information flows across the organization.
Establishing effective data governance frameworks and selecting compatible software solutions are key to overcoming this challenge. It’s also prudent to equip your teams with corporate big data modeling and management systems training.
- Cost of Implementation: The costs associated with digital transformation are substantial, especially for large-scale implementations that cover various areas of production, logistics, and customer service. Budget constraints can slow the adoption of essential technologies, leading to delayed returns on investment. Companies require careful financial planning to balance immediate costs with long-term gains, identifying high-impact areas where digital transformation can yield measurable benefits. Corporate financial planning skills are ideal for empowering businesses to optimize financial resources and guide strategic decisions, to foster long-term financial stability and growth.
- Measuring ROI and Success: Digital transformation in manufacturing involves multiple processes, making it difficult to measure direct return on investment (ROI). Companies often face challenges in defining key performance indicators (KPIs) that accurately reflect the impact of transformation efforts. Identifying relevant metrics, such as cost savings, productivity gains, and customer satisfaction, and tracking them consistently is essential for evaluating success and making necessary adjustments.
- Confusing Marketplace: The rapid expansion of digital technologies IoT, AI, cloud, and big data offers manufacturers numerous choices, creating a complex tech landscape that can make digital transformation daunting. The vast array of vendors and tools can overwhelm organizations, leading to decision paralysis and stalled projects, especially with pressure from stakeholders for progress.
Choosing the wrong tech can waste resources and create compatibility issues, hindering transformation. Manufacturers should begin with a needs assessment to clarify priorities, and then evaluate options based on scalability, integration, and cost. Engaging industry experts, and trusted vendors, and participating in industry forums can also provide insights to navigate the marketplace and make informed, strategic tech investments.
- Sustaining Innovation and Continuous Improvement: The rapid pace of technological change demands a culture of continuous innovation and improvement. However, once initial digital transformation projects are complete, many companies struggle to sustain momentum and keep up with new developments. Building a culture that embraces continuous improvement and regularly assesses emerging technologies is crucial to remain competitive and maximize the benefits of transformation.
Successfully navigating these challenges requires manufacturing companies to adopt a proactive, flexible approach, balancing innovation with practical strategies that address industry-specific obstacles. Each step in overcoming these challenges builds a foundation for a resilient, future-ready manufacturing environment.
Recent Success Stories of Digital Transformation in Manufacturing
In recent years, several manufacturing companies have successfully implemented digital transformation strategies that have drastically improved their operational efficiency, product quality, and sustainability. The examples below highlight manufacturers who embraced advanced technologies like AI, IoT, and automation, reshaping their production processes and gaining a competitive edge. These case studies provide insights into how these companies navigated their digital transformation journey, the positive impact on their operations, and the valuable lessons they learned along the way.
Ford Case Study: How Ford Developed the New Explorer Using Formlabs SLA and SLS 3D Printers
How They Implemented Additive Manufacturing at Ford’s PD Merkenich Facility
Ford’s PD Merkenich facility in Cologne integrated advanced 3D printing technologies into their vehicle development process. The center uses SLA, SLS, and FDM 3D printers to rapidly prototype vehicle components, helping to shorten development times. Ford was a pioneer in Europe, being the first to use stereolithography (SLA) 3D printing in 1994. Today, the facility is equipped with various 3D printing technologies, including Formlabs’ Form 4 and Fuse 1+ 30W printers, to create design prototypes and functional parts.
These technologies allow Ford to quickly validate designs and make changes based on feedback, which is crucial in the increasingly compressed timelines for product development, particularly as they transition to electric vehicles (EVs).
The Impact on Product Development and Competitive Advantage
The use of additive manufacturing at Ford’s PD Merkenich facility has had a profound impact on their development cycles and competitive edge. The speed and flexibility provided by 3D printing allow Ford to rapidly produce high-quality prototypes, significantly reducing the time needed to iterate on designs. For example, they can now produce exterior and interior parts like the Explorer’s rearview mirror assembly in a matter of hours instead of days.
This ability to quickly adjust designs and print functional parts has helped Ford maintain a competitive position in the fast-evolving automotive market. Their commitment to electrification by 2030 requires such agility, and 3D printing has become a vital tool for keeping up with the industry's shift to EVs.
Key Takeaways from Ford’s Approach to 3D Printing
- Faster Iteration and Testing: The adoption of SLA and SLS 3D printing has dramatically improved the speed of prototyping and part testing, reducing development cycles and allowing Ford to keep up with the industry's rapid pace.
- Cost Efficiency: Additive manufacturing has cut down on traditional tooling costs, allowing Ford to produce rapid tooling inserts for injection molding at a fraction of the cost and time required for traditional metal tooling.
- Increased Flexibility: With technologies like SLS 3D printing, Ford can produce complex mechanical parts that would otherwise be impossible to manufacture using traditional methods. This flexibility is essential for testing parts in real-world conditions.
- Collaboration Across Facilities: Ford’s global teams, including those in Dunton Technical Centre (UK) and Cologne, collaborate closely to create a unified approach to rapid prototyping and vehicle development.
Case Study: Enhancing Compliance Through Digital Transformation with a Paperless Quality Logbook in Pharma:
How a Pharma Giant Implemented a Digital Logbook Solution for Pharma Compliance
A U.S.-based pharmaceutical manufacturing company, part of a major global company, faced challenges with paper-based logbooks in their manufacturing and packaging operations. To streamline operations and enhance GMP compliance, they partnered with SCW.AI to implement a Digital Logbook solution. The solution adheres to global regulations such as FDA 21 CFR Part 11 and Eudralex volume 4 and integrates features like e-signatures, audit trails, and out-of-specification notifications. The Digital Logbook system automated workflows, ensuring accurate and efficient data entry, and reducing reliance on manual processes.
The Impact on Compliance, Efficiency, and Operational Excellence
By digitizing over 500 logbooks and handling 22,400 log entries per year, the company significantly reduced its manual workload and the error rate. The digital solution streamlined data entry, enhanced audit readiness, and made data more accessible to production executives and quality managers. Compliance was strengthened, enabling faster reporting, approvals, and decision-making. Additionally, automated workflows minimized human error, while real-time data collection improved both operational efficiency and data-driven decision-making, ultimately leading to quicker turnaround times for regulatory compliance.
Key Takeaways from the Digital Transformation in Pharma Operations
- Streamlined Data Entry: The Digital Logbook simplified data entry with automated sections and predefined workflows, reducing the workload for operators and improving data accuracy.
- Enhanced Compliance and Audit Readiness: Automated compliance tracking and built-in audit trails ensured the company remained audit-ready at all times.
- Improved Decision-Making: Consolidated and real-time data reporting enabled faster and more accurate decision-making, with improved root cause analysis for production issues.
- Reduced Manual Errors and Increased Efficiency: Automated workflows reduced manual errors, allowing resources to focus on more value-added tasks and improving overall operational efficiency.
These cases highlight how digital transformation can reshape manufacturing by introducing scalable, efficient, and production-centered solutions. For manufacturers aiming to stay competitive, focusing on technologies that enable agility, improve operational efficiency, and streamline processes is essential.
What Does the Future Hold for Digital Transformation in Manufacturing?
What will manufacturing facilities look like in the future? Cobots will work alongside human operators, improving safety and productivity through seamless interaction. With predictive maintenance powered by the Industrial Internet of Things (IIoT) and sensors, factories will transition from reactive to proactive equipment management, using data analytics to foresee issues and reduce downtime. Digital twins will enable virtual simulations and real-time process optimization, allowing manufacturers to detect and resolve bottlenecks swiftly.
In automated warehouses, robotics, guided by sophisticated algorithms, will streamline inventory management and order fulfillment with high precision. Meanwhile, AI-powered visual inspection systems will transform quality control, leveraging machine learning for accurate, rapid defect detection throughout the production line. These interconnected advancements will yield autonomous factories that operate efficiently with minimal human intervention, leveraging vast amounts of data to refine every aspect of production paving the way for a resilient, agile, and highly efficient manufacturing landscape.
Frequently Asked Questions
Conclusion
The journey of digital transformation in the manufacturing industry presents both a compelling opportunity and a significant challenge. As industries evolve to adopt new technologies like AI, IoT, additive manufacturing, and blockchain, manufacturers must consider the readiness and skill level of their workforce. Are your teams equipped to embrace these technological advancements? The success of your digital transformation will be determined by how well your employees can leverage these cutting-edge tools to improve production efficiency, enhance quality control, and drive sustainability.
Edstellar can support this transformation by providing training solutions specifically designed for digital transformation leadership in the manufacturing sector. From mastering IoT and predictive maintenance to understanding the capabilities of digital twins and augmented reality, Edstellar ensures your team is well-prepared to handle the demands of a tech-driven manufacturing environment. Investing in workforce development is not just a requirement, it’s a strategic move that will help your organization achieve operational excellence, reduced downtime, and increased customer satisfaction.
As digital technologies redefine the manufacturing industry, having employees skilled in data analytics, machine learning, and automation will help you stay competitive. Proficient teams are more capable of embracing change, which directly impacts the overall success of digital transformation strategy. Upskilling employees ensures smoother adoption of these technologies, leading to greater operational efficiency, cost savings, and improved product quality.
Embracing digital transformation leadership in manufacturing means more than just adopting new technologies; it’s about fostering a culture of innovation within your team. The right training empowers your employees to navigate new systems, optimize processes, and contribute to the development of smarter, more sustainable products. As the industry continues to transform, having a skilled, adaptable workforce will be key to staying ahead in the market and achieving long-term success.
Explore High-impact instructor-led training for your teams.
#On-site #Virtual #GroupTraining #Customized
Edstellar Training Catalog
Explore 2000+ industry ready instructor-led training programs.
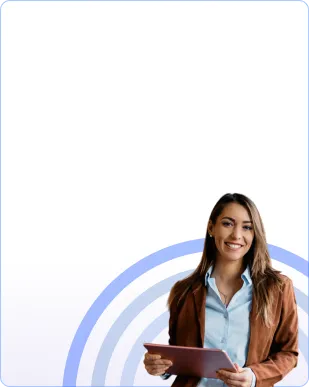
Coaching that Unlocks Potential
Create dynamic leaders and cohesive teams. Learn more now!
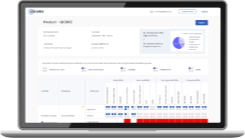
Want to evaluate your team’s skill gaps?
Do a quick Skill gap analysis with Edstellar’s Free Skill Matrix tool
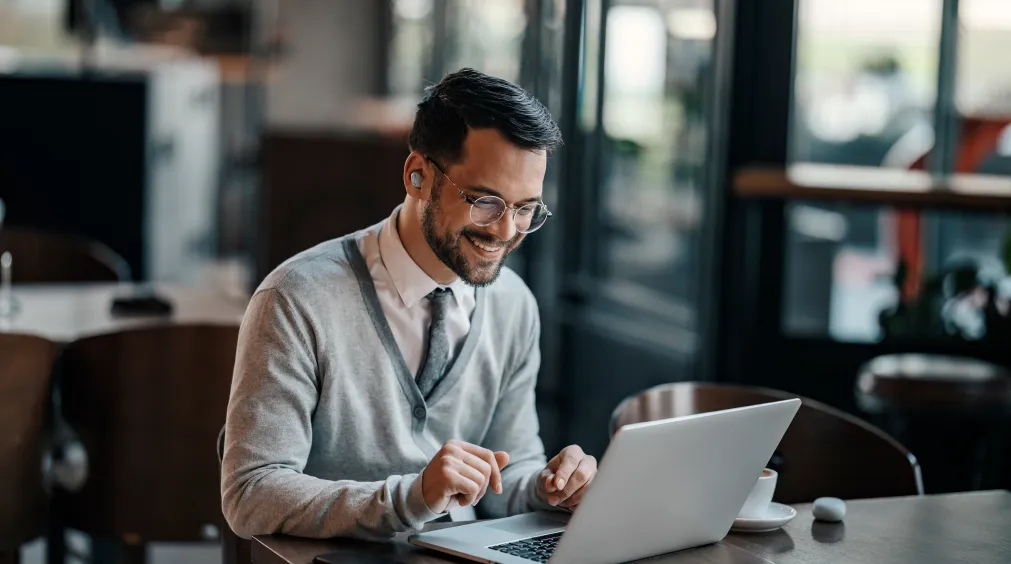
Transform Your L&D Strategy Today
Unlock premium resources, tools, and frameworks designed for HR and learning professionals. Our L&D Hub gives you everything needed to elevate your organization's training approach.
Access L&D Hub Resources